Versatile Cell-Free Protein Synthesis Systems Based on Chinese Hamster Ovary Cells
Lena Thoring, Stefan Kubick
Cell-free protein synthesis
CHO cells
Continuous exchange cell-free systems
Difficult-to-express proteins
In vitro protein production
Internal ribosomal entry sites
Linear expression templates
Abstract
We present an alternative production platform for the synthesis of complex proteins. Apart from conventionally applied protein production using engineered mammalian cell lines, this protocol describes the preparation and principle of cell-free protein synthesis systems based on CHO cell lysates. The CHO cell-free system contains endogenous microsomes derived from the endoplasmic reticulum, which enables a direct integration of membrane proteins into a nature like milieu and the introduction of posttranslational modifications. Different steps of system development are described including the cultivation of CHO cells, cell harvesting and cell disruption to prepare translationally active CHO cell lysates. The requirements for DNA templates and the generation of linear DNA templates suitable for the CHO cell-free reaction is further depicted to underline the opportunity to produce different protein variants in a short period. This experimental setup provides a basis for high-throughput applications. The productivity of the CHO cell-free systems is further increased by using a non-canonical translation initiation due to the attachment of an internal ribosomal entry site of the Cricket paralysis virus (CRPV IRES) to the 5´ UTR of the desired gene. In this way, a direct interaction of the IRES structure with the ribosome facilitates a translation factor independent initiation of translation. Cell-free reactions were performed in fast and efficient batch reactions leading to protein yields up to 40 μg/mL. The reaction format was further adjusted to a continuous exchange CHO cell-free reaction (CHO CECF) to prolong reaction time and thereby increase the productivity of the cell-free systems. Finally, protein yields up to 1 g/L were obtained. The CHO CECF system represents a sophisticated resource to address structural and functional aspects of difficult-to-express proteins in fundamental and applied research.
Steps
3.1 Biomass Production
Initially culture CHO -K1 cells in shake flask starting with a density between 0.5 and 0.7 × 106cells/mL. Cultivation conditions are set to a temperature of 37°C
, a CO2concentration of 5% and a shaking speed of 100 RPM.
For biomass production, the stirred tank bioreactor is inoculated with CHO-K1 cells precultured in shake flasks at an initial density of around 1.0 × 106cells/mL.
The fermentation process can be performed in repeated batch or perfusion mode:
The repeated batch process includes a cell growth phase of approximately 2 days to obtain cell densities between 4 and 5 × 106cells/mL grown in the exponential growth phase, which is followed by the cell harvest. A defined volume of cell suspension remains in the cultivation vessel to start a second cycle of batch cultivation. The repeated batch is performed for 3 cycles.
To increase the produced biomass, a perfusion fermentation process can be applied to the CHO cell lysate preparation protocol. For this, CHO cells are inoculated at a density of 1 × 106cells/mL, perform a batch based process until a density between 3–4 × 106cells/mL is reached and start perfusion mode using a perfusion rate of 0.5 RV/day (RV: reactor volume).

3.2 Cell Harvest, Disruption and Preparation of Translationally Active CHO Cell Lysates
Exponentially grown CHO cells are harvested by centrifugation using a fixed angle rotor or a continuous flow rotor depending on the volume of cell suspension.
After harvesting cells are washed with HEPES based wash buffer ( see Materials section 2.1 "Cell Cultivation", item 10 ) to remove culture medium components.
Before cell disruption, suspend CHO cells in wash buffer to obtain a final density of approximately 1.0 × 108cells/mL.
For preparation of translationally active CHO lysate, which contains endogenous microsomes, a mild disruption procedure is required. Therefore, disrupt CHO cells mechanically by passing the suspended cell pellet through a 20-gauge needle or disruption using high-pressure homogenization ( see Note 11 ).
A raw CHO lysate is further prepared by differential centrifugation at 10000x g,4°C
. This step is required for the removal of cell debris, cell nuclei and cellular organelles ( see Note 12 ). Raw lysate can be flash frozen using liquid nitrogen and stored at −80 °C prior to further recondition steps.
Raw lysate is applied to a preequilibrated Sephadex G-25 column and elute using wash buffer ( see Materials section 2.1 "Cell Cultivation", item 10 ). Collect fractions of 1 mL and quantify RNA concentration by absorbance estimation using the NanoDrop 2000C. Pool fractions displaying an absorbance above 1 at 260 nm.
Pooled fractions are treated with micrococcal S7 nuclease (10 U/mL) to digest and remove endogenous mRNA. The S7 nuclease has a calcium dependent digestion activity, therefore add 1 mM of CaCl2 to the enzyme containing eluate and incubate for 0h 2m 0s
at Room temperature
.
The enzymatic reaction is inactivated using the Ca2+chelating regent EGTA (6.7 mM final concentration).
The energy regenerating enzyme creatine kinase (100 μg/mL final concentration) is added to the lysate to enable the regeneration of ATP using creatine phosphate as a phosphate donor.
The final translationally active CHO lysate is flash frozen and stored at -80°C
( see Note 13 ).
3.3 Generation of Linear Expression Templates
The gene of interest is amplified using gene specific adapter primers harboring an overlap to the 5′- and 3′- regulatory sequences.
The 5′- regulatory sequences, which contains a stem loop for stabilization, the T7 RNA promotor and the CRPV IGR IRES, are amplified using a regulatory sequence donor vector, Reg-F and CRPV-R primer.
Subsequently, verify the presence of both PCR products on agarose gel prior to their fusion and the generation of the final linear expression template ( see Note 14 ).
Fusion PCR is performed by application of both previously generated DNA fragments (gene fragment and 5′- regulatory fragment) in an equimolar amount to the reaction and supplementation of regulatory primers (Reg-F and Reg-R). A high-fidelity DNA dependent polymerase is used for DNA amplification to enable a high correctness of produced DNA sequence by low misincorporation rates and proof reading activities.
Analyze the produced linear PCR fragment on an agarose gel prior to the application to the cell-free reaction ( see Note 15 ).
Different signal peptides, purification tags and fluorescence tags can be integrated into the DNA sequences by the previously described procedure. For this, overlap sequences and regulatory primer pairs need be adapted to the individual requirements.
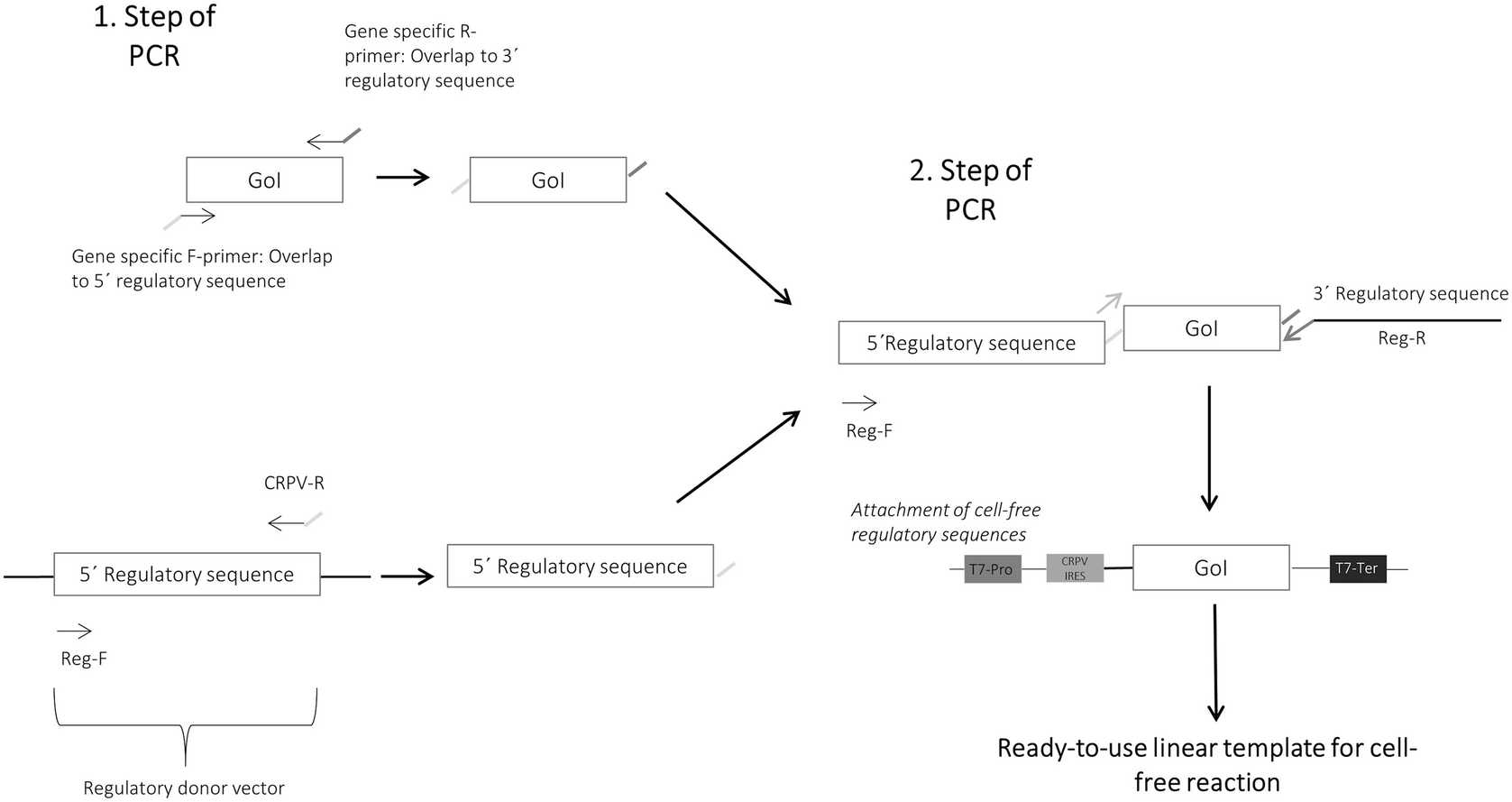
3.4 Preparation of Circular Plasmid Templates
Transformation of the desired plasmid template into E. coli JM109 cells is performed by electroporation using a 1 mM cuvette and a Biorad electroporation system.
Transformed cells are plated on agar-antibiotic plats for E. coli clone growth. Transformed E. coli cell stocks are stored in glycerol at -80°C
.
E. coli cell clone is picked and inoculated into a shake flask containing LB medium and the appropriate antibiotics and cultured at 37°C
.
Amplified plasmid DNA is isolated from E. coli overnight culture using the PureLink HiPure Plasmid Prep Kit ( see Note 16 ).
Concentration of isolated plasmid DNA was analyzed at an absorbance of 260 nm using the Nanodrop 2000 C. A 260/280 purity value around 1.8 is required for further applicability of the plasmid DNA to a cell-free protein synthesis reaction.
Gene integration is evaluated by treatment of isolated plasmid DNA with restriction enzymes and separation of obtained DNA fragments by agarose gel electrophoresis. DNA fragment size is estimated using Clone Manager Software.
The DNA sequence is further verified by gene sequencing using M13-F and M13-R primers.
3.5 Cell-Free Synthesis in a Batch-Formatted Reaction
All required components for cell-free protein synthesis are thawed On ice
prior to their use in the reaction ( see Note 17 ).
Batch formatted CHO cell-free reactions are performed in Eppendorf tubes containing reaction volumes from 20 μL up to 500 μL. Reports of prokaryotic cell-free systems show the possibility for process scale up to 100 L reaction volume [20] .
To prevent RNase contamination, pipette CHO cell-free reactions using filter tips.
The preparation of the cell-free CHO batch reaction is performed On ice
. The general principle of the CHO lysate based cell-free protein synthesis is illustrated in Fig. 3a.
The transcription/translation coupled CHO cell-free batch reaction is composed of 40% CHO cell lysate, 10% translation buffer and 20% energy buffer.
Typically, 20 nM of plasmid DNA is added to the reaction but the optimal concentration depends on the applied vector backbone ( see Note 18 ).
To enable transcription of mRNA , supplement 1 U/μL T7 RNA polymerase to the CHO cell-free reaction.
For further analysis of produced proteins, 14C leucine (specific radioactivity: 66.67 dpm/pmol) is added to the reaction and cotranslationally incorporated into the synthesized proteins.
Reaction volume is adjusted by supplementation with Millipore water to the final volume.
Optimization experiments included a further increase of T7 RNA polymerase to 3 U/μL and the supplementation of molecular crowding reagents (PEG, Ficoll) ( see Note 19 ).
All components were pipetted directly to the reaction while adjusting the volume by adding ddH2O. Standard conditions present in a batch-formatted CHO cell-free reaction are summarized in Table 1.
Table 1
List of standard reaction conditions present in a batch-formatted CHO cell-free system: optimized conditions are indicated in bold letters
A | B |
---|---|
Component/Parameter | CHO batch reaction conditions |
Cell lysate | 40% (vol/vol) |
HEPES KOH, pH 7.6 | 30 mM |
KoAc | 150 mM |
Mg(OAc)2 | 3.9 mM |
ATP | 1.75 mM |
CTP,GTP,UTP | 0.3 mM |
m7G(ppp)G cap (cap I) | 0.1 mM |
Amino acids | 100 μM |
14C Leucine | 66.67 dpm/pmol |
Plasmid concentration | 20 nM |
T7 RNA polymerase | 1 U/μL (3 U/μL) |
DTT | 2.5 mM |
PEG 1500 | 2% |
Temperature | 30 °C |
Agitation | 600 RPM |
Reaction time | 3 h |
Ready prepared cell-free translation mixture is incubated for 3h 0m 0s
at 30°C
using a thermomixer.
The CHO cell-free translation mixture can be directly used for further analysis of the produced protein. Cell-free synthesized proteins can be applied to various assays. Radio labeled proteins can be quantified using TCA precipitation followed by scintillation measurement.
Molecular weight and protein modifications can be analyzed by separation of acetone-precipitated proteins on SDS-PAGE followed by autoradiography.
Figure 3 shows exemplary CHO cell-free synthesis of membrane protein and ion channel KvAP. Functional membrane proteins are integrated into the ER derived microsomes of CHO lysate. Microsomes can be separated by centrifugation (16000x g,4°C
). Proteins integrated into the microsomes can be enriched by a repetitive addressing procedure. For this, a batch based cell-free reaction is initially performed followed by the separation of microsomal fraction. The separated microsomes are dissolved in a freshly prepared cell-free reaction depleted from microsomes, which enables the enrichment of translocated proteins into microsomes. This procedure is performed for three repetitive cycles. A schematic overview is illustrated in Fig. 3b. The produced membrane protein KvAP shows the formation of monomeric and multimeric structures in the autoradiograph (Fig. 3c). An increase in produced membrane protein is detected in the microsomal fraction (Fig. 3d) ( see Note 20 ).
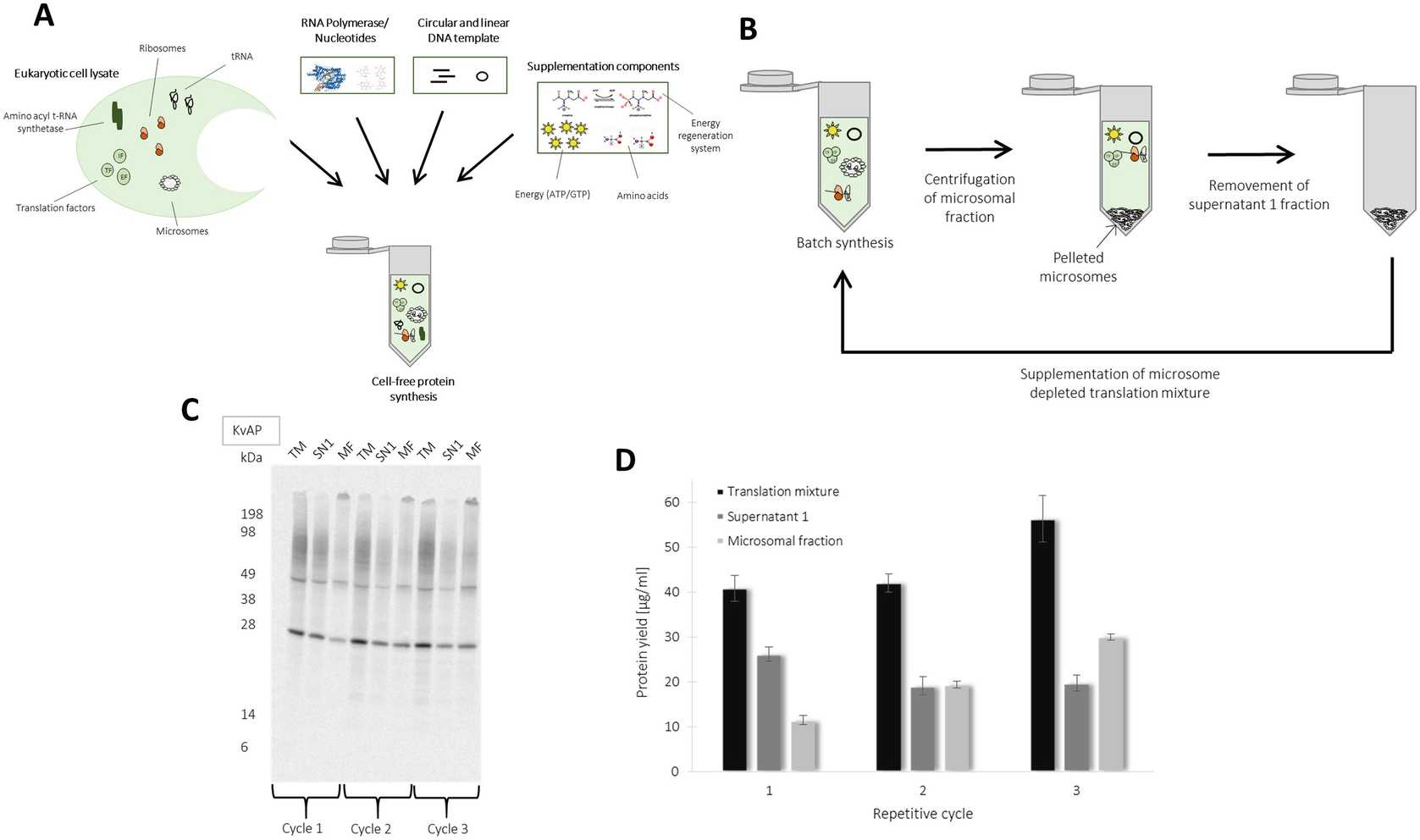
3.6 High-Yield Production of Proteins Using a Continuous Exchange Cell-Free System
As reported for the batch formatted cell-free reaction, all components are thawed On ice
prior to their use in the reaction ( see Note 17 ).
The preparation of CECF reaction is performed On ice
.
The CHO continuous exchange cell-free reaction is performed in a two chamber device consisting of a reaction chamber (50 μL) and a feeding chamber (1000 μL). A general scheme of CHO CECF reaction is depicted in Fig. 4a . The reaction chamber contains a general cell-free reaction, the feeding chamber includes additional energy components. Both chambers are separated by a semipermeable membrane and due to diffusion gradients energy components are continuously delivered to the reaction chamber and inhibitory byproducts are removed from the reaction chamber. Thereby, protein production time is prolonged resulting in an increased protein yield. Analysis of reactor membrane cut-off by CECF synthesis of membrane protein EGFR fused to a C-terminal eYFP, results in an optimal protein yield using a membrane cut-off between 10 and 14 kDa in comparison to smaller cut-offs (3–8 kDa) (Fig. 4b) ( see Note 21 2 1).
Feeding and reaction mix are prepared separately.
Table 2
List of standard reaction conditions present in a CHO CECF system
A | B | C | D |
---|---|---|---|
Component/Parameter | CHO CECF reaction conditions | Reaction mix | Feeding mix |
Cell lysate | 40% (Vol/Vol) | × | |
HEPES KOH, pH 7.6 | 30 mM | × | × |
KoAc | 150 mM | × | × |
Mg(OAc)2 | 3.9 mM | × | |
Mg(OAc)2 | 22 mM | × | |
ATP | 1.75 mM | × | × |
CTP,GTP,UTP | 0.3 mM | × | × |
Amino acids | 100 μM | × | × |
14C Leucine | 9.9 dpm/pmol | × | × |
Sodium azide | 0.02% | × | |
Plasmid | 30 nM | × | × |
T7 RNA polymerase | 1 U/μL | × | |
DTT | 2.5 mM | × | × |
Caspase inhibitor Ac-DEVD-CMK | 30 μM | × | × |
Temperature | 30 °C | × | × |
Agitation | 600 RPM | × | × |
Reaction time | 48 h | × | × |
The feeding mix consists of 1× translation buffer and 1× energy buffer harboring the conditions described in Table 2. Additionally, 0.02% sodium azide ( see Note 22 ), caspase inhibitor Ac-DEVD-CMK (30 μM), 14C leucine (9.9 dpm/pmol), and ddH2O (filling up to 1000 μL) are added to complete the feeding mixture.
The reaction mix is then prepared. The optimized conditions of the reaction mix differ from the standard CHO cell-free batch reaction and are illustrated in Table 2. Essential parameters which differ from the standard conditions are the concentration of Mg(OAC) (22 mM), creatine phosphate (18.5 mM), caspase inhibitor Ac-DEVD-CMK (30 μM), plasmid concentration (30 nM),and 14C leucine (9.9 dpm/pmol).
The reaction mixture is transferred into the dialysis device followed by the feeding mix.
The device is sealed with plastic foil and place into a thermomixer C for incubation at 30°C
, 48h 0m 0s
.
After finishing the CECF synthesis, the sealing is removed and reaction mixture is transferred into an Eppendorf tube for further analysis.
Like reported for the batch based cell-free reaction, reaction mixture can be directly used for the analysis of the produced proteins. Different batches of CECF synthesized membrane protein EGFR were quantified and analyzed using autoradiography (Fig. 4 c).
The quantification was performed using 3µL
for hot TCA precipitation and further analysis by scintillation measurement. Typically, protein yields of approximately 1000 μg/mL are obtained. An autoradiograph of EGFR shows the expected molecular weight at around 170 kDa.
Protein glycosylation can be monitored by adding 3 nM 14C mannose to the CHO CECF reaction.
After finishing cell-free protein synthesis, acetone precipitate 14C mannose labeled sample and can be directly applied to SDS-PAGE .
The dried gel is analyzed by autoradiography.
For the purpose of verifying the specificity of protein glycosylation, a treatment of CHO CECF sample using glycosidases PNGaseF (NEB) and EndoH (NEB) is performed according to the manufacturer’s protocol. The results show the specificity of EGFR glycosylation performed in the CHO CECF system (Fig. 4d).
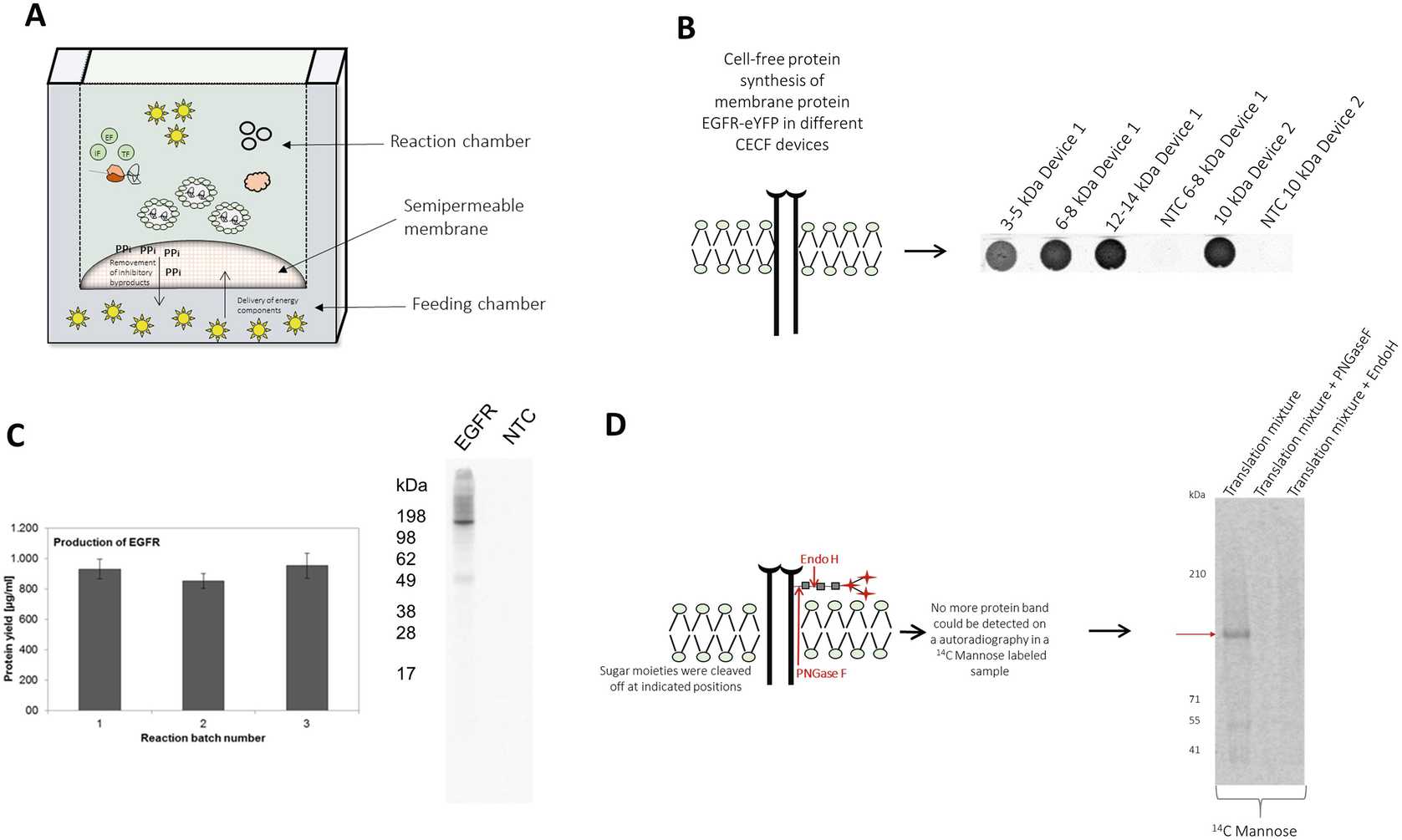
3.7 Application of Linear Expression Templates to CHO Cell-Free Systems
For the application of PCR products to the CHO cell-free reactions, perform standard batch formatted as well as CECF reactions. Plasmid DNA is replaced by previously prepared linear expression template.
The productivity of batch cell-free systems based on linear expression templates are strongly dependent on the concentration of applied PCR-product. Figure 5a shows the dependency of PCR product concentration on the received protein yield in a batch formatted CHO cell-free reaction for the production of secreted protein EPO. A maximum protein yield is obtained by the application of 12.5nanogram per microliter (ng/μL)
to the batch formatted CHO cell-free protein synthesis system.
An increase in T7 RNA polymerase concentration from 1 U/μL to 3 U/μL results in a significant increase in protein yield in the batch system. Protein yields up to approximately 12 μg/mL of secretory EPO were obtained by a combined increase of T7 RNA polymerase and PCR product concentration (Fig. 5a) ( see Note 23 ).
The application of linear DNA templates to the CHO CECF system requires an increase of T7 RNA polymerase and PCR product concentration as reported for the batch formatted system. A maximum protein yield of 350 μg/mL of membrane protein EGFR was obtained using 3 U/μL and 54nanogram per microliter (ng/μL)
.
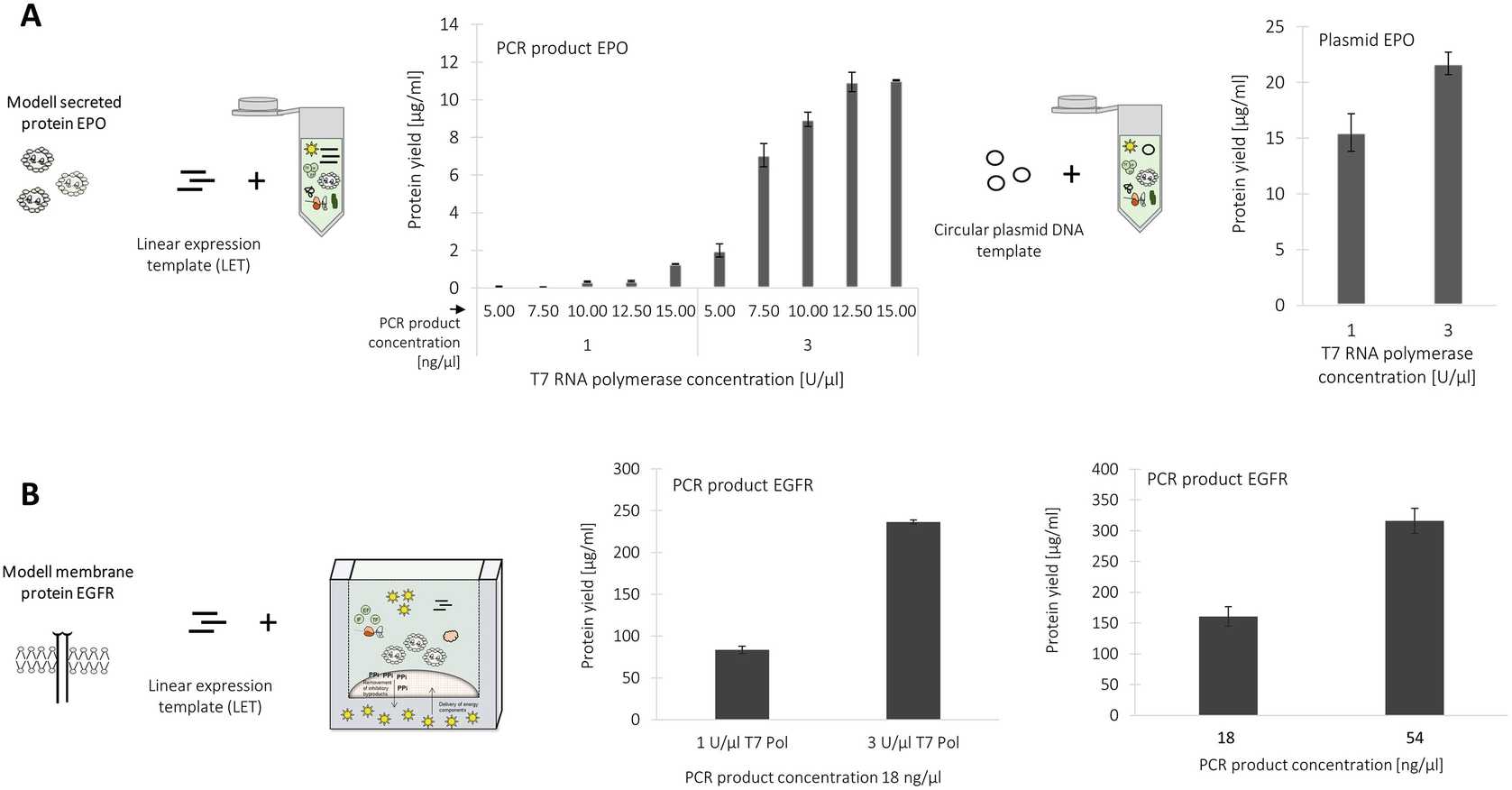