Past human stone tool performance: experiments to test the influence of raw material variability and edge angle design on tool function
Walter Gneisinger, Lisa Schunk, Ivan Calandra, Joao Marreiros, Anja Cramer
Controlled experiments
Keilmesser
tool durability
tool efficiency
edge angle
Middle Palaeolithic
Neanderthal technology
Abstract
The goal of this sequential experiment was to test tool performance of Late Middle Palaeolithic Keilmesser by examining two relevant characteristics concerning their edge design: the raw material and the edge angle.
To do so, a controlled, mechanical setup was used. The samples and the contact material were standardised to limit the number of confounding factors. As tasks, unidirectional cutting and carving movements were performed. The edge angle values for the experimental standard samples were chosen to reflect the calculated edge angles from the analysed Keilmesser .
Steps
Documentation of the archaeological tools
The research question behind this here presented experiment is based on archaeological artefacts, so-called Keilmesser from the Late Middle Palaeoltihic. The artefacts are from the sites of Balver Höhle, the Upper site of Buhlen (both Germany) and Grotte de Ramioul (Belgium). For more information about the sites see the following (exemplary) references:
3D scanning
In total 175N
Keilmesser were analysed and scanned with an AICON smartScan-HE R8 from the manufacturer Hexagon (software version OptoCat 2018R1). The S-150 FOV (field of view) used has a point-to-point distance of 33 µm.
Equipment
Value | Label |
---|---|
smartScan-HE R8 | NAME |
3D structured light scanner | TYPE |
AICON | BRAND |
- | SKU |
S-150 FOV, resolution of 33 µm | SPECIFICATIONS |
Software
Value | Label |
---|---|
OptoCat | NAME |
Hexagon Manufacturing Intelligence Software | DEVELOPER |
2018R1 | VERSION |
The scanning settings are identical to the following protocol, and details can be found there:
The editing steps to create a closed 3D model are also the same as in the protocol mentioned above and were executed with GOM inspect, a free software for 3D measurement data.
Software
Value | Label |
---|---|
GOM Inspect | NAME |
Hotfix 2, Rev. 111729, build 2018-08-22 | OS_NAME |
GOM | DEVELOPER |
https://www.gom.com/de-de/produkte/gom-inspect-suite | LINK |
2018 | VERSION |
Edge angle calculation
The edge angle measurements on the 3D models of the Keilmesser were taken with 3D-EdgeAngle . For details about the method see (publication of the forthcoming paper):
For calculating the edge angles, the following parameters were applied:
- "2-lines" measuring procedure
- the length of the line was defined with 2 mm
- 10 mm as distance to the intersection
- only sections two to eight were used
Mean values were calculated in R, a free software and programming language for statistical computing and graphics.
Software
Value | Label |
---|---|
R Studio Desktop | NAME |
The R Studio, Inc. | DEVELOPER |
https://www.rstudio.com/products/RStudio/ | LINK |
1.1.463 | VERSION |
See "analysis_EA_Keilmesser" within the following repository on GitHub:
https://github.com/lschunk/PastHuman_StoneToolPerformance.git
Or in open access on Zenodo:
Sample preparation
Standardised tools
24 experimental standard samples were produced for the experiment:
6 x 35°
6 x 35°
6 x 45°
6 x 45°
Raw material
Baltic flint:
Southern Sweden (secondary deposit):
Silicified schist:
Balver Höhle
Buhlen
Blanks
Raw material nodules/ blocks (step #2.1) were first cut into rectangular cuboids (blanks) of the following dimensions:
10mm
25mm
60mm
Equipment
Value | Label |
---|---|
Goliath 450 | NAME |
Lapidary rock saw | TYPE |
Steinschleifmaschinen & Lapidary tools Ltd. | BRAND |
- | SKU |
- | SPECIFICATIONS |
a) cut 10mm
slices
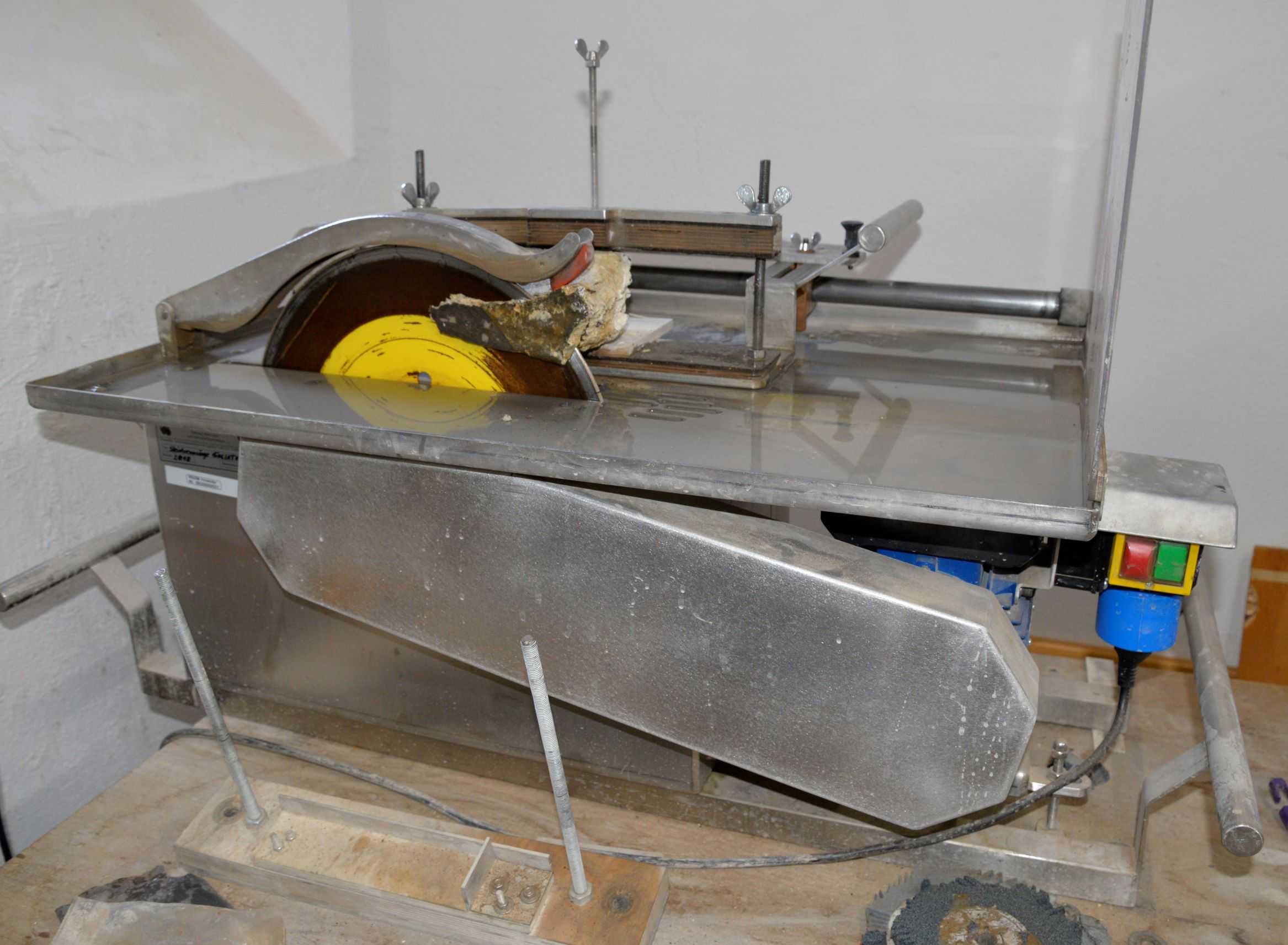
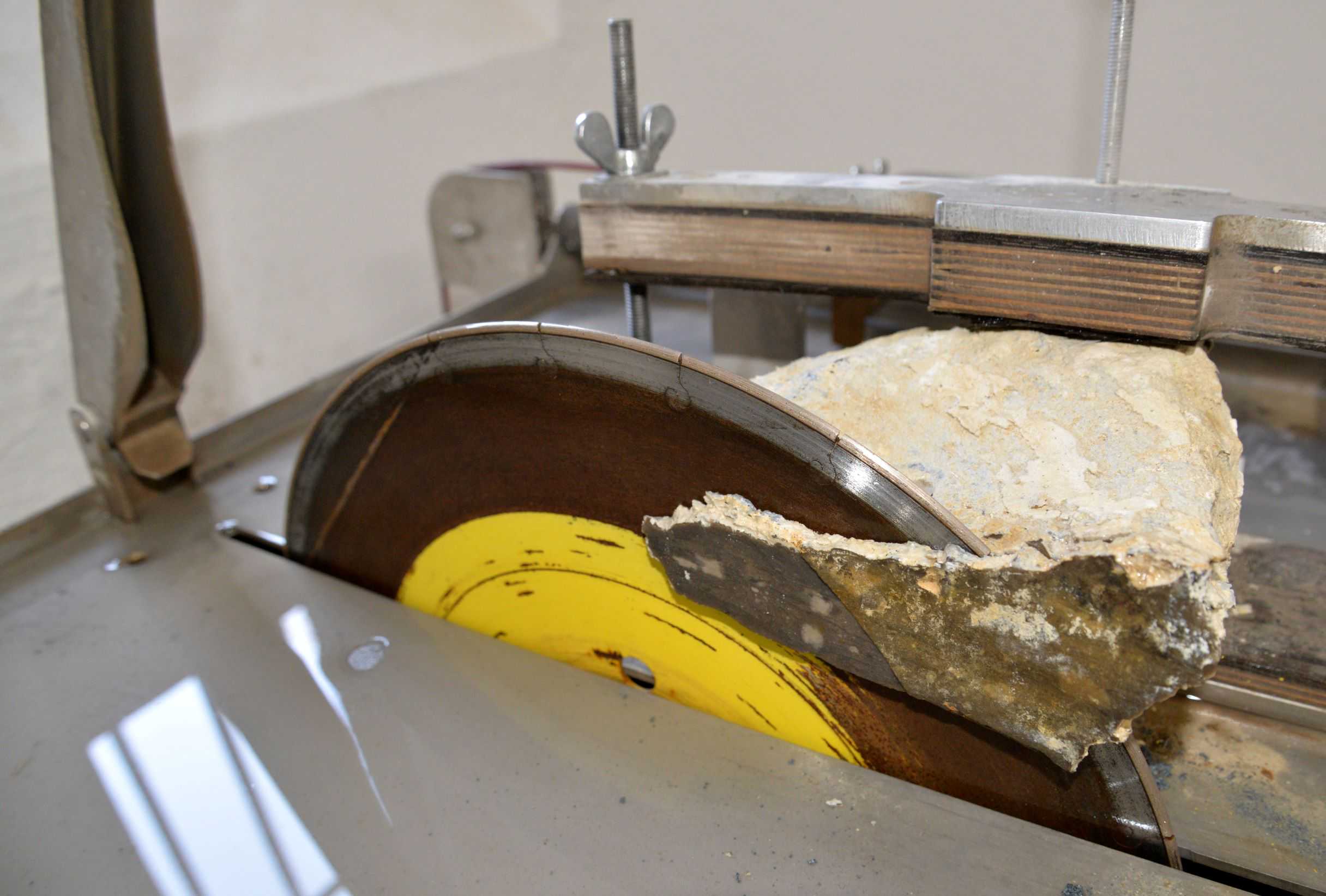
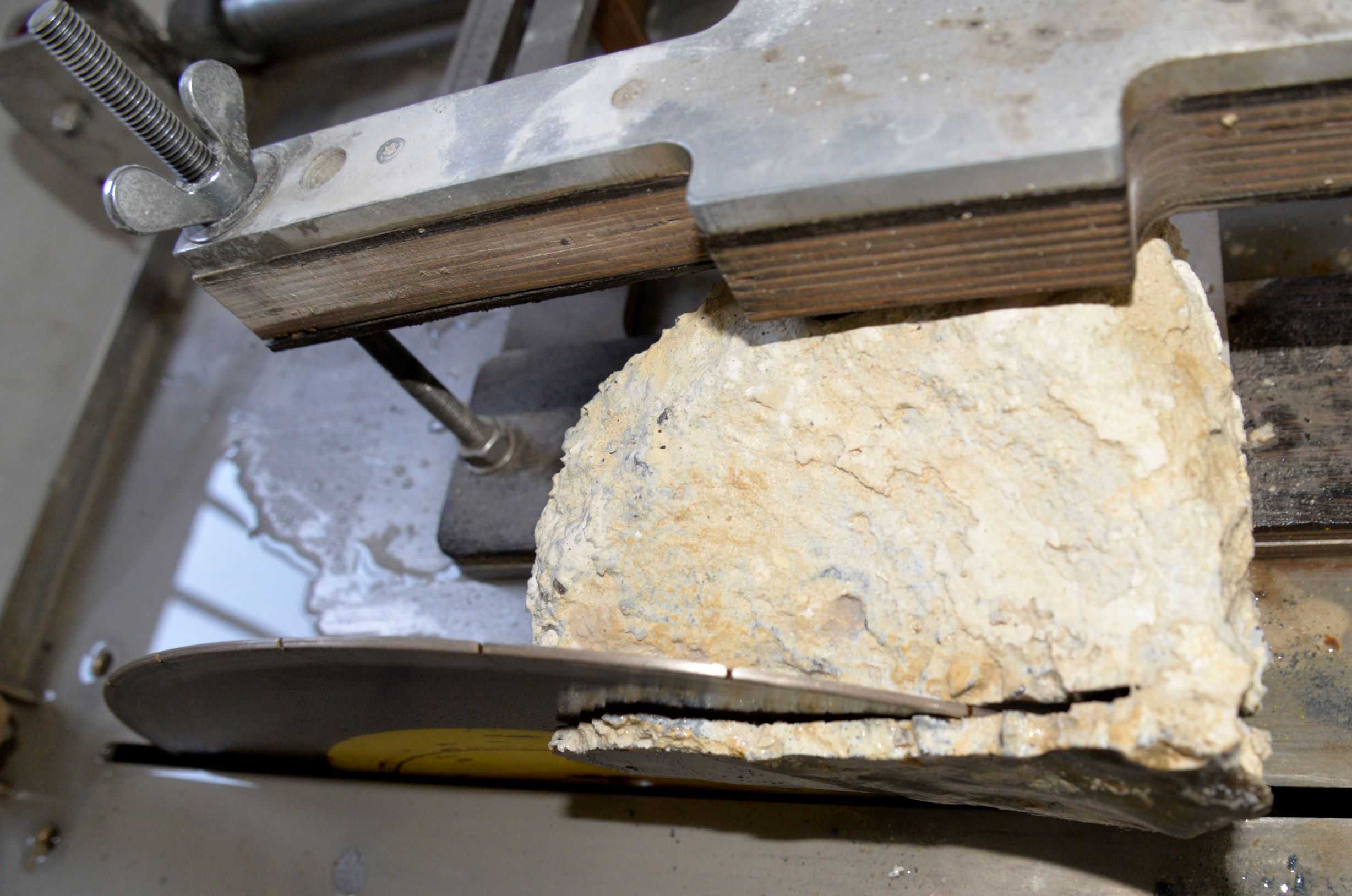
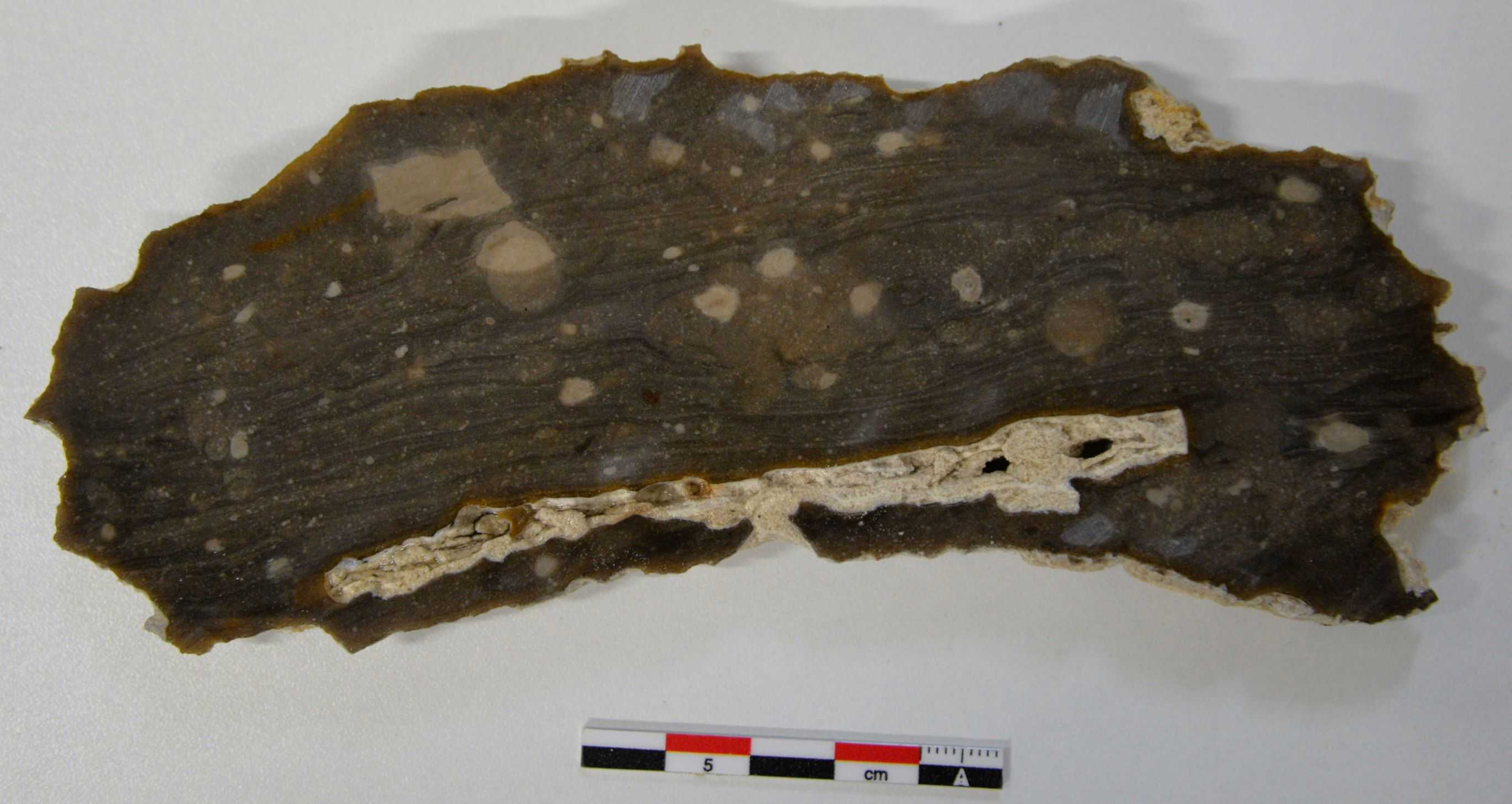

b) cut slices into blanks
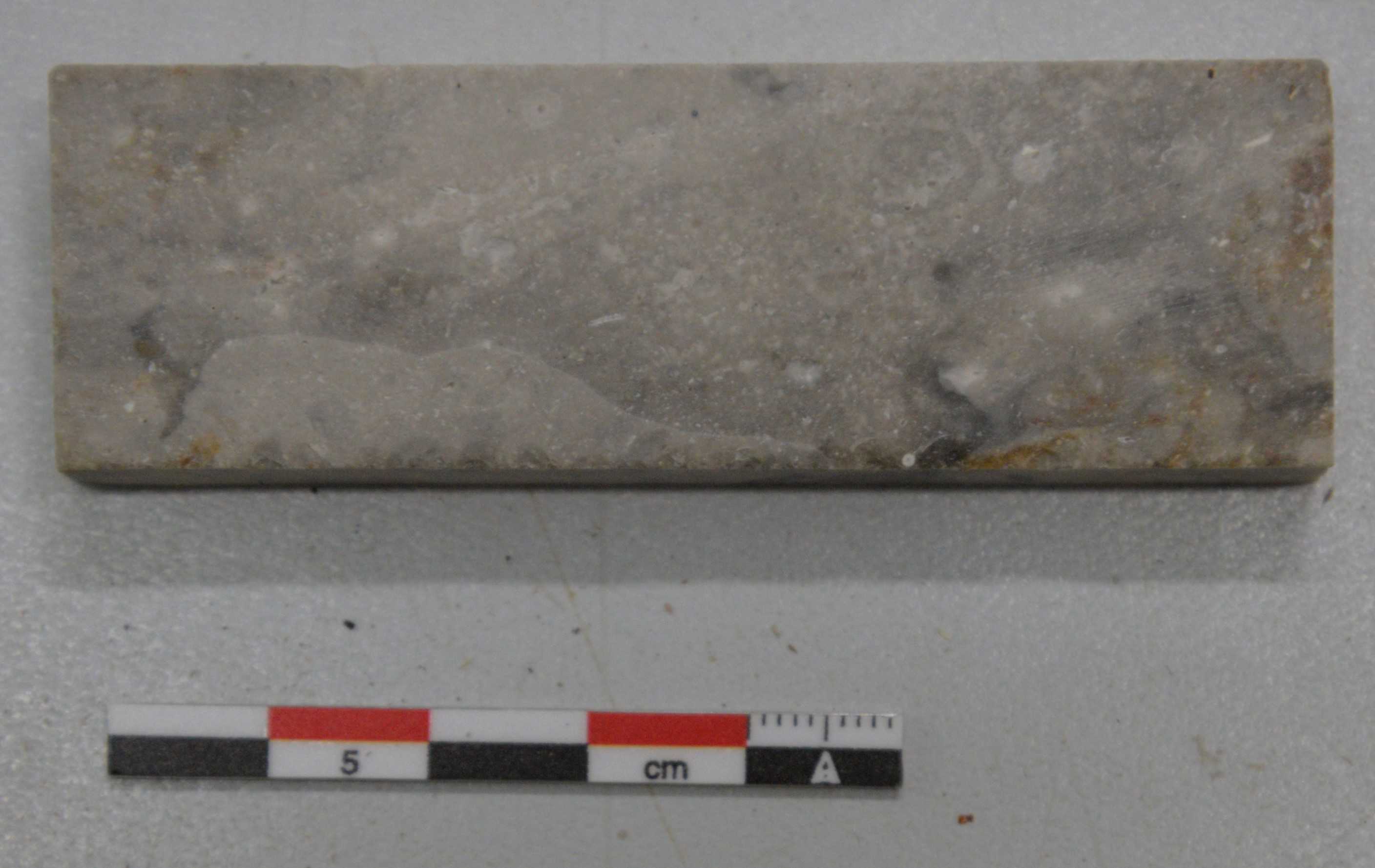
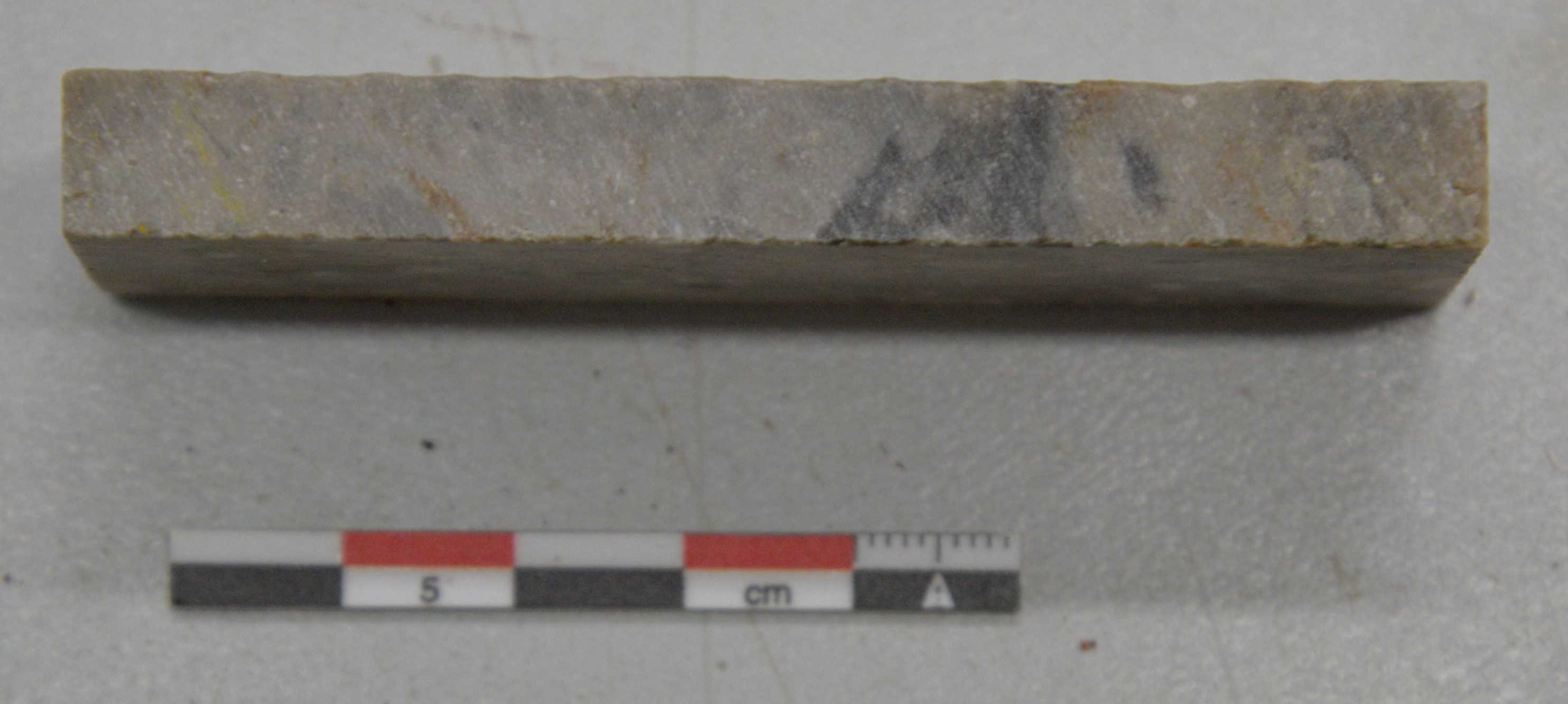
Hardness measurement
The hardness of the blanks (step #2.2) was measured with a Leeb rebound hardness tester.
Equipment
Value | Label |
---|---|
Equotip 550 | NAME |
Portable hardness tester | TYPE |
Proceq | BRAND |
- | SKU |
Leeb C probe | SPECIFICATIONS |
The blanks were placed on a stable base of sufficient mass (here a polished granite slab of about 20kg
). Since the samples did not fulfill the requirements for minimum sample size and weight, coupling paste was used between the sample and the base. Each blank was measured ten times to insure and test intra-blank variability.
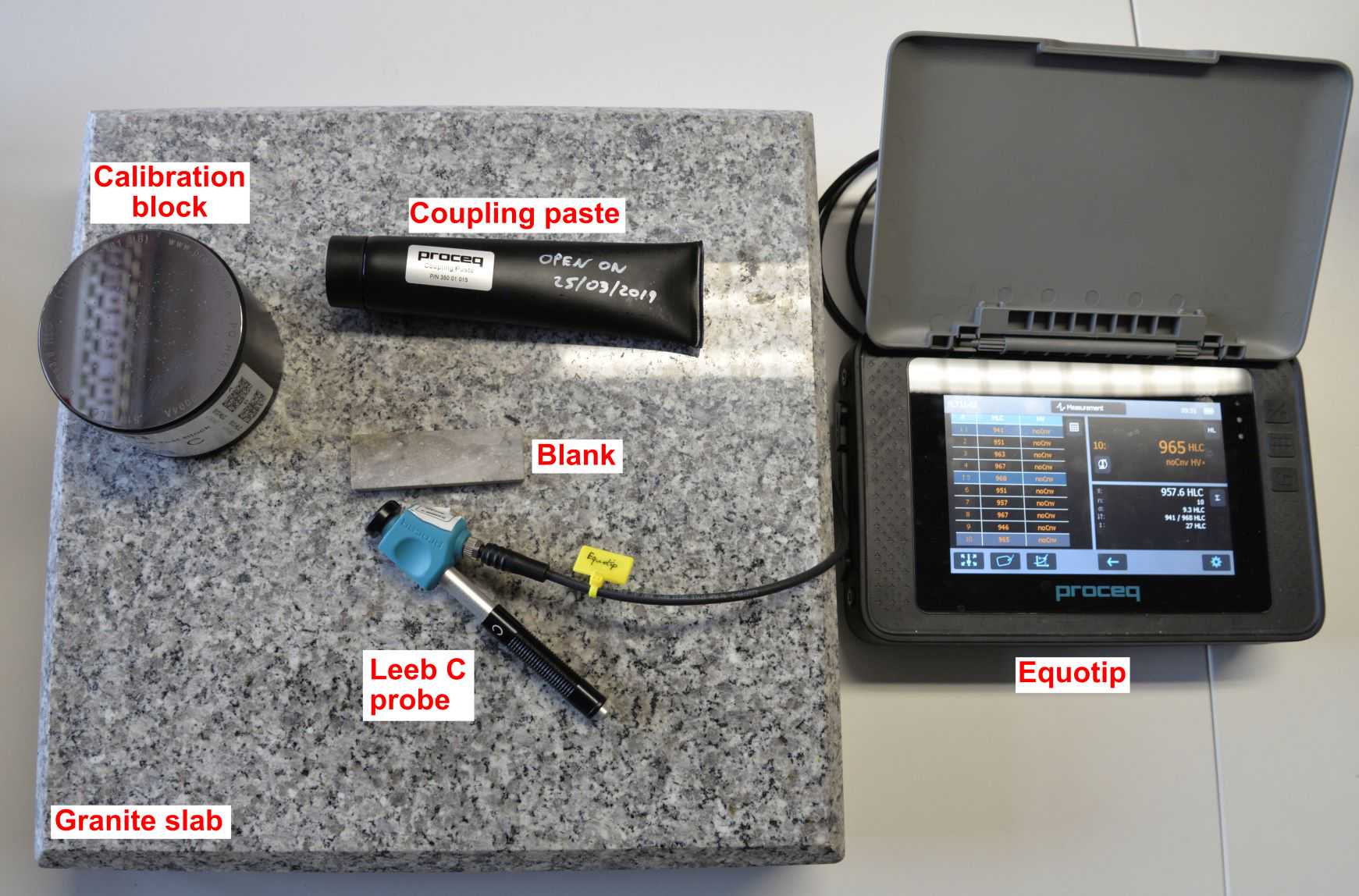
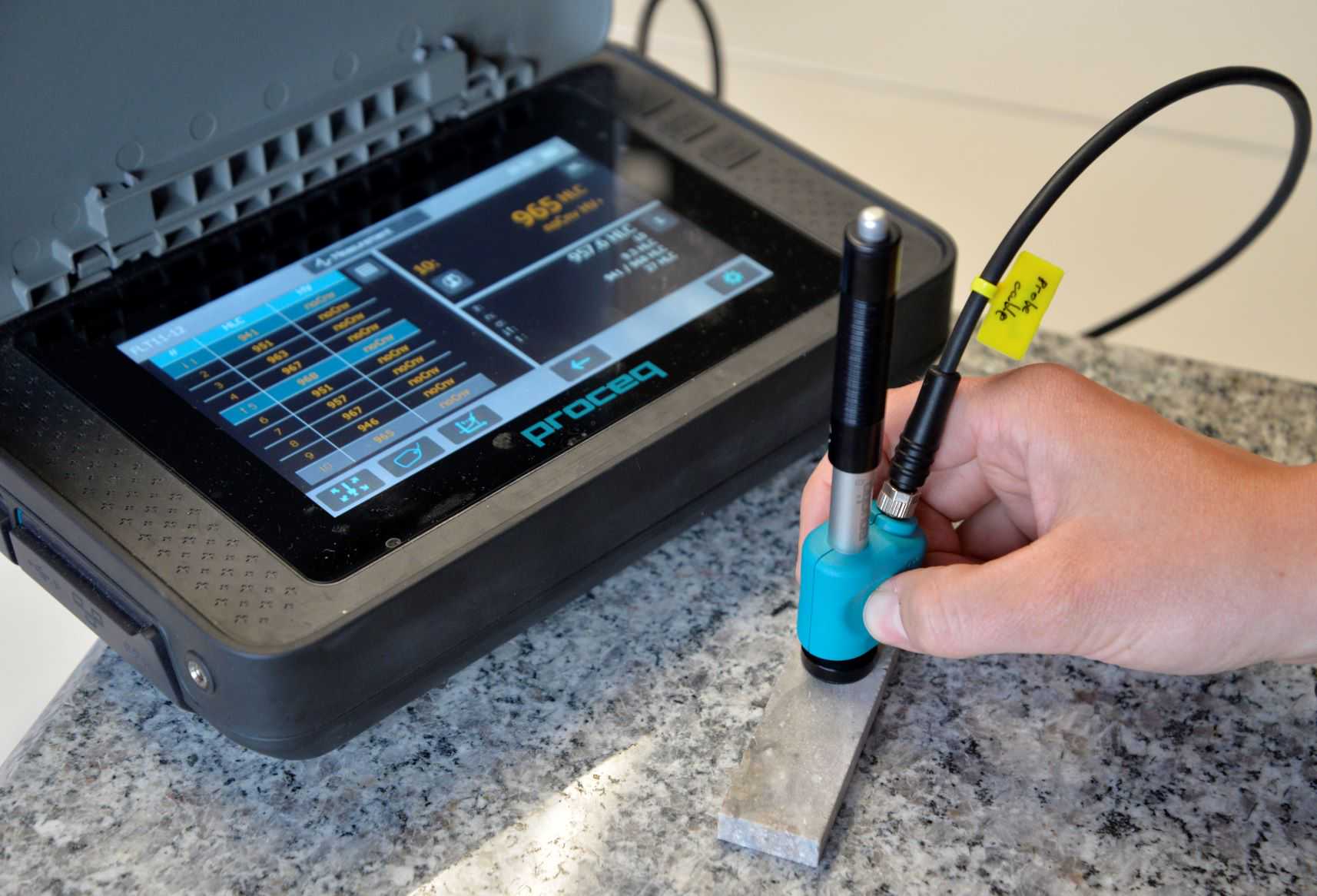
Edge angle
One end of the blanks (step #2.2) was cut to produce samples with a 35°
/ 45°
, with the following dimensions:
10mm
25mm
30mm
Equipment
Value | Label |
---|---|
310 CP | NAME |
Diamond band saw | TYPE |
Exact | BRAND |
- | SKU |
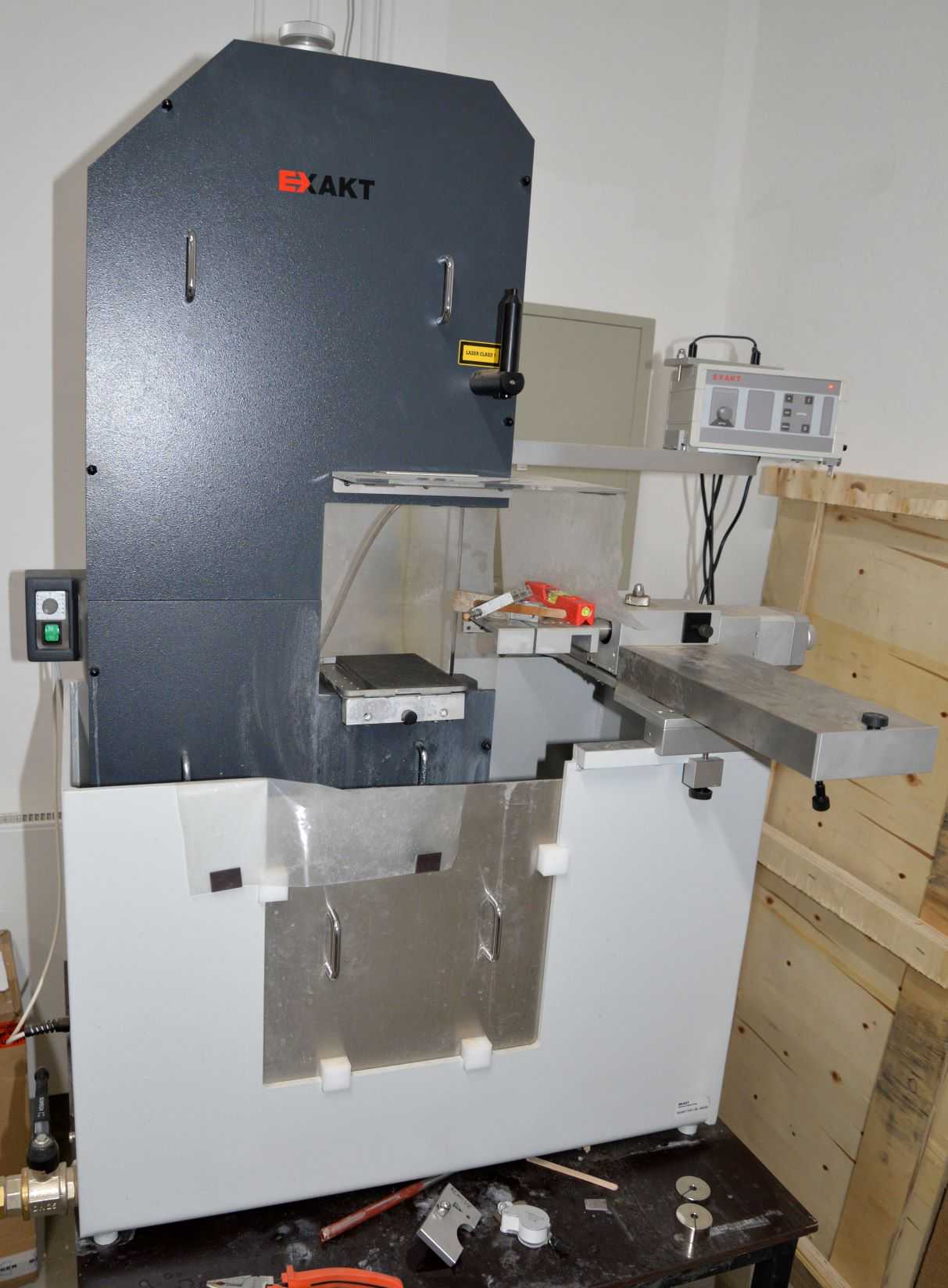
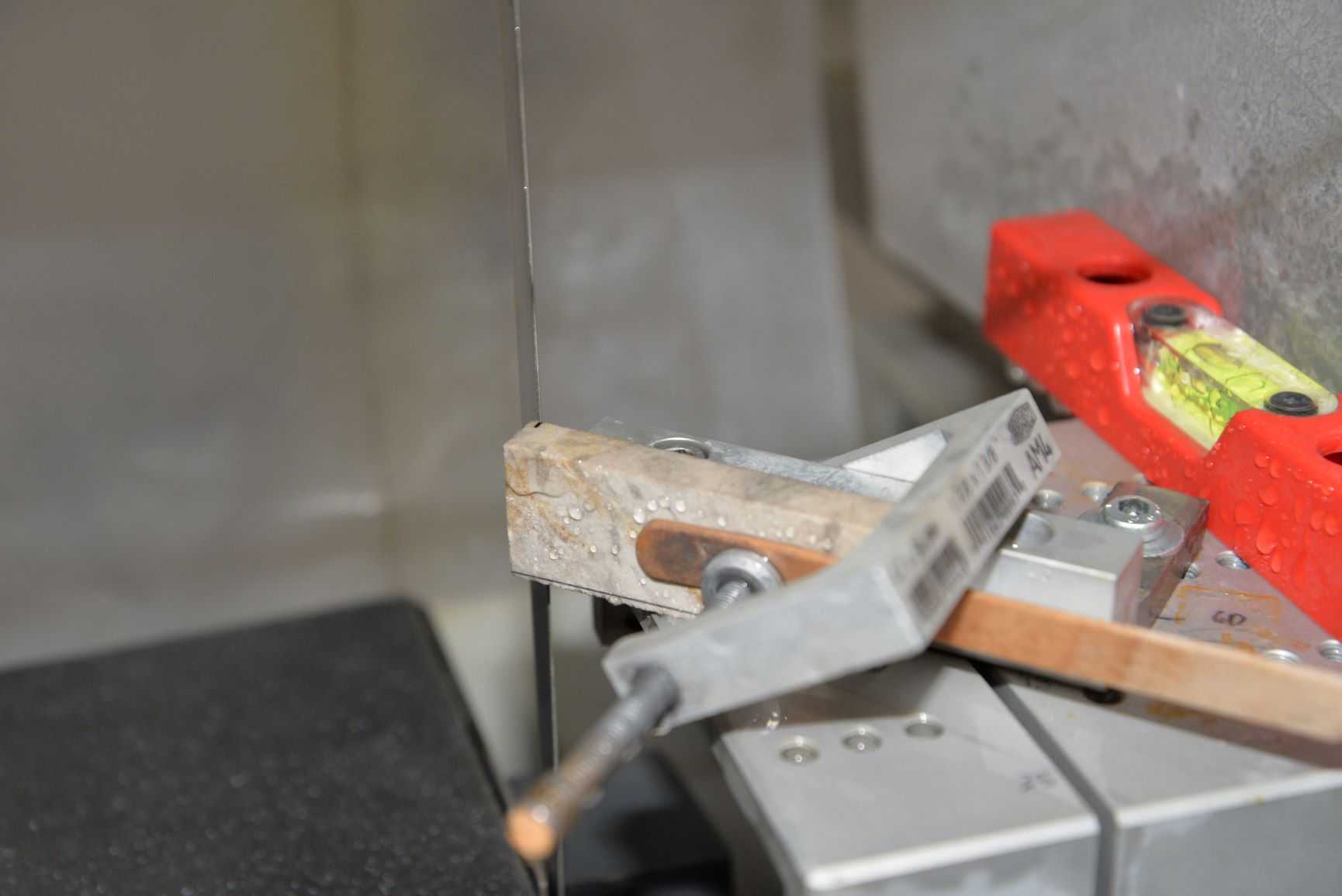
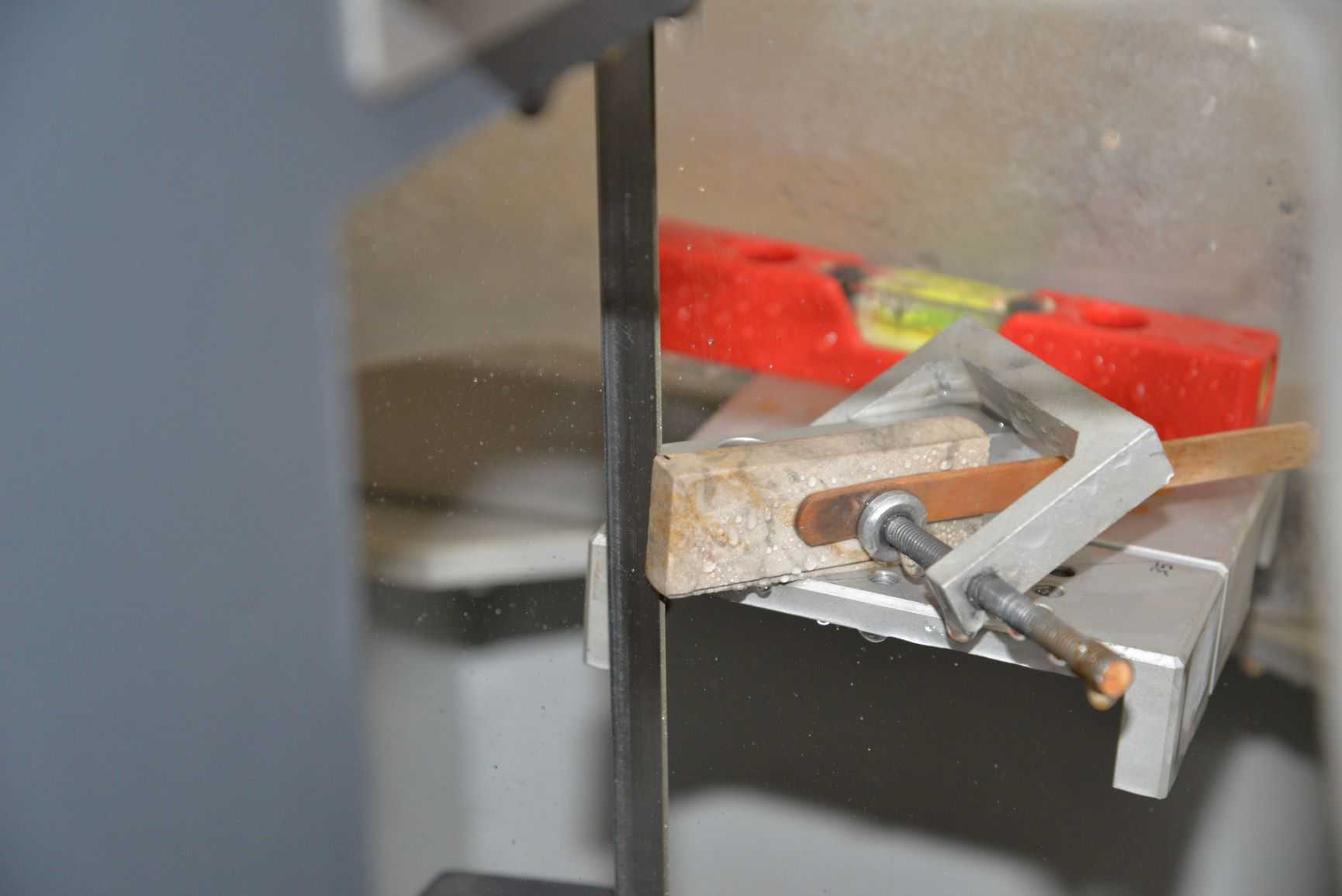
<img src="https://static.yanyin.tech/literature_test/protocol_io_true/protocols.io.3byl4kr6ovo5/duehbgyf7.jpg" alt="Experimental standard sample without chamfered edge, view of side A (corresponding to the "dorsal" side of bifacial lithic artefact; here: flint)." loading="lazy" title="Experimental standard sample without chamfered edge, view of side A (corresponding to the "dorsal" side of bifacial lithic artefact; here: flint)."/>
<img src="https://static.yanyin.tech/literature_test/protocol_io_true/protocols.io.3byl4kr6ovo5/duejbgyf7.jpg" alt="Experimental standard sample without chamfered edge, view of side D (corresponding to the "lateral" side of bifacial lithic artefact; here: flint)." loading="lazy" title="Experimental standard sample without chamfered edge, view of side D (corresponding to the "lateral" side of bifacial lithic artefact; here: flint)."/>
Chamfered edge
To avoid catastrophic breakage of the edge during experiments, the leading edge of the experimental standard samples (step #2.4) was chamfered to a 45°
(see #2.6 for photos).
Equipment
Value | Label |
---|---|
310 CP | NAME |
Diamond band saw | TYPE |
Exact | BRAND |
- | SKU |
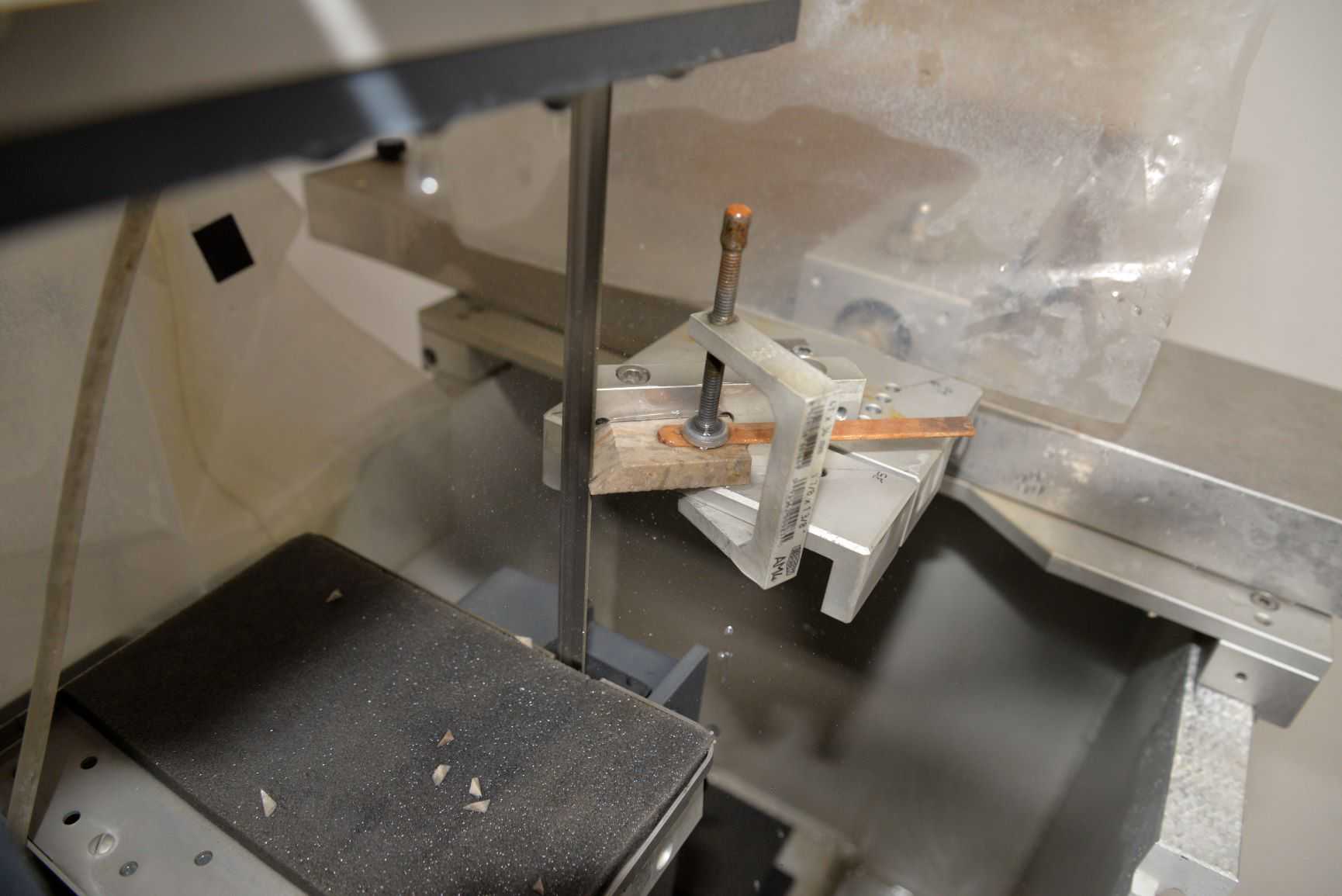
The cut with the band saw left a small burr between the two adjacent surfaces at the edge of the chamfered surface and the lateral side D. This burr was manually removed with a diamond drill bit in a mini drill.
Coordinate system
Three ceramic beads were adhered onto each side of the cutting edge to provide a coordinate system on each side.
<img src="https://static.yanyin.tech/literature_test/protocol_io_true/protocols.io.3byl4kr6ovo5/dyfcbgyf7.jpg" alt="Final experimental standard sample with beads, view of side A (corresponding to the "dorsal" side of bifacial lithic artefact; here: flint)." loading="lazy" title="Final experimental standard sample with beads, view of side A (corresponding to the "dorsal" side of bifacial lithic artefact; here: flint)."/>
<img src="https://static.yanyin.tech/literature_test/protocol_io_true/protocols.io.3byl4kr6ovo5/dye4bgyf7.jpg" alt="Final experimental standard sample with beads, view of side C (corresponding to the "ventral" side of bifacial lithic artefact; here: flint)." loading="lazy" title="Final experimental standard sample with beads, view of side C (corresponding to the "ventral" side of bifacial lithic artefact; here: flint)."/>
For details, see:
Summary of the standard sample production
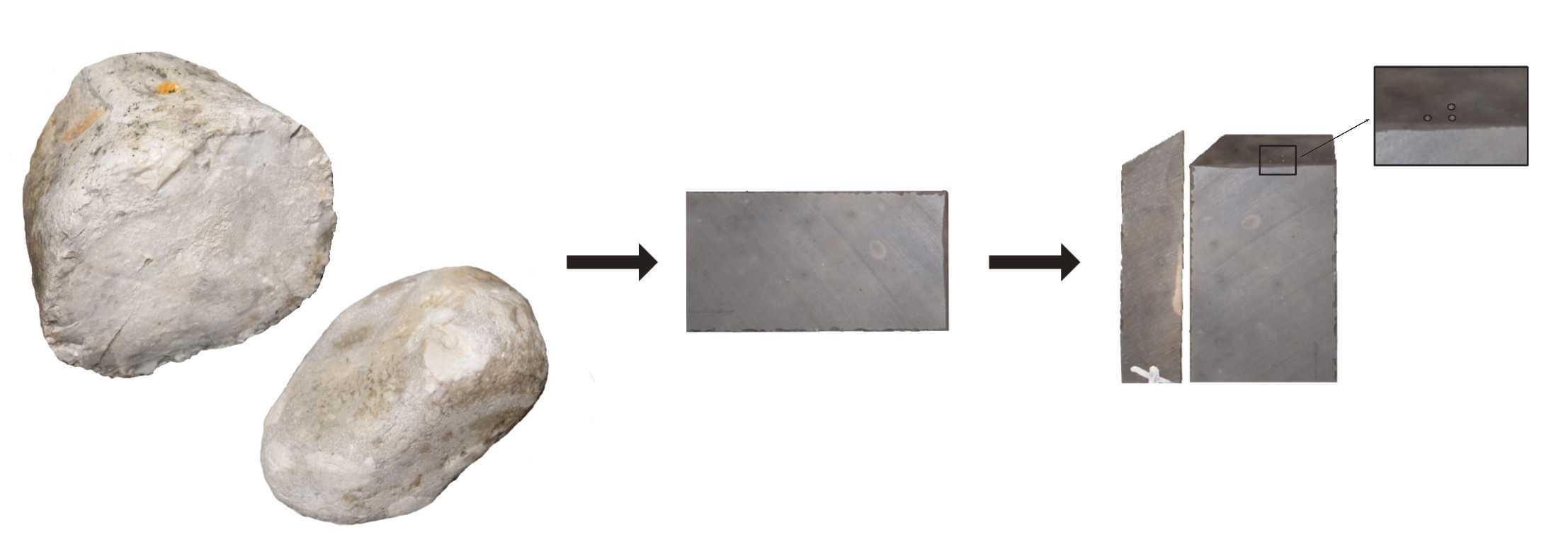
Cleaning
100mL
1Mass / % volume
Equipment
Value | Label |
---|---|
Sonorex Digitec DT255H | NAME |
Heated ultrasonic bath | TYPE |
Bandelin | BRAND |
- | SKU |
4.5 L | SPECIFICATIONS |
40°C
0h 5m 0s
Contact material
Mechanical device
General settings
Linear unidirectional movements (cutting & carving): 2000strokes
split in 4cycles
.
The cycles are defined by the following number of strokes:
1strokes
to 50strokes
51strokes
to 250strokes
251strokes
to 1000strokes
1001strokes
to 2000strokes
Experimental setup
Equipment
Value | Label |
---|---|
SMARTTESTER | NAME |
Modular material tester | TYPE |
Inotec AP | BRAND |
- | SKU |
recorded values with the time stamps: - for each drive: position, speed, acceleration (+ deceleration) - penetration depth with distance sensor - apllied force with force sensor 1 (strain gauge sensor) - friction with force sensor 2 (strain gauge sensor) | SPECIFICATIONS |
Linear movement from start point to end point:
5kg
(= ~ 50 N)
170mm
600mm/s
4000mm/s2
10Hz
(for each channel)
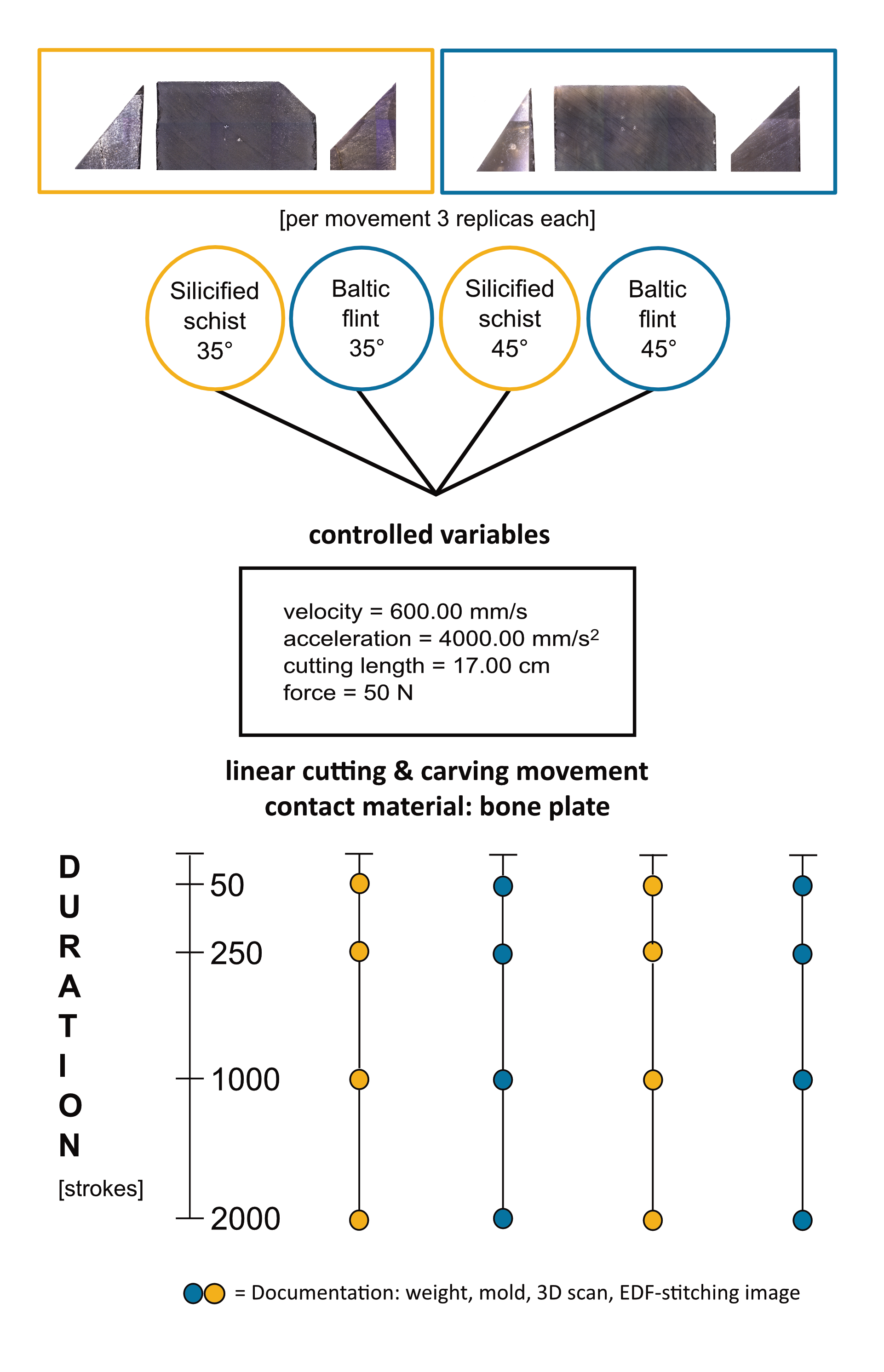
Setup sample holder
The length of the spring of the sample holder was adjusted to compensate for the weight of the sample holder (without dead weights and sample).
Adjust the position of the upper end of the spring on the rail, so that:
- the sample holder almost touches the frame, and
- at the same time, there should be no pull from the spring onto the sample holder.
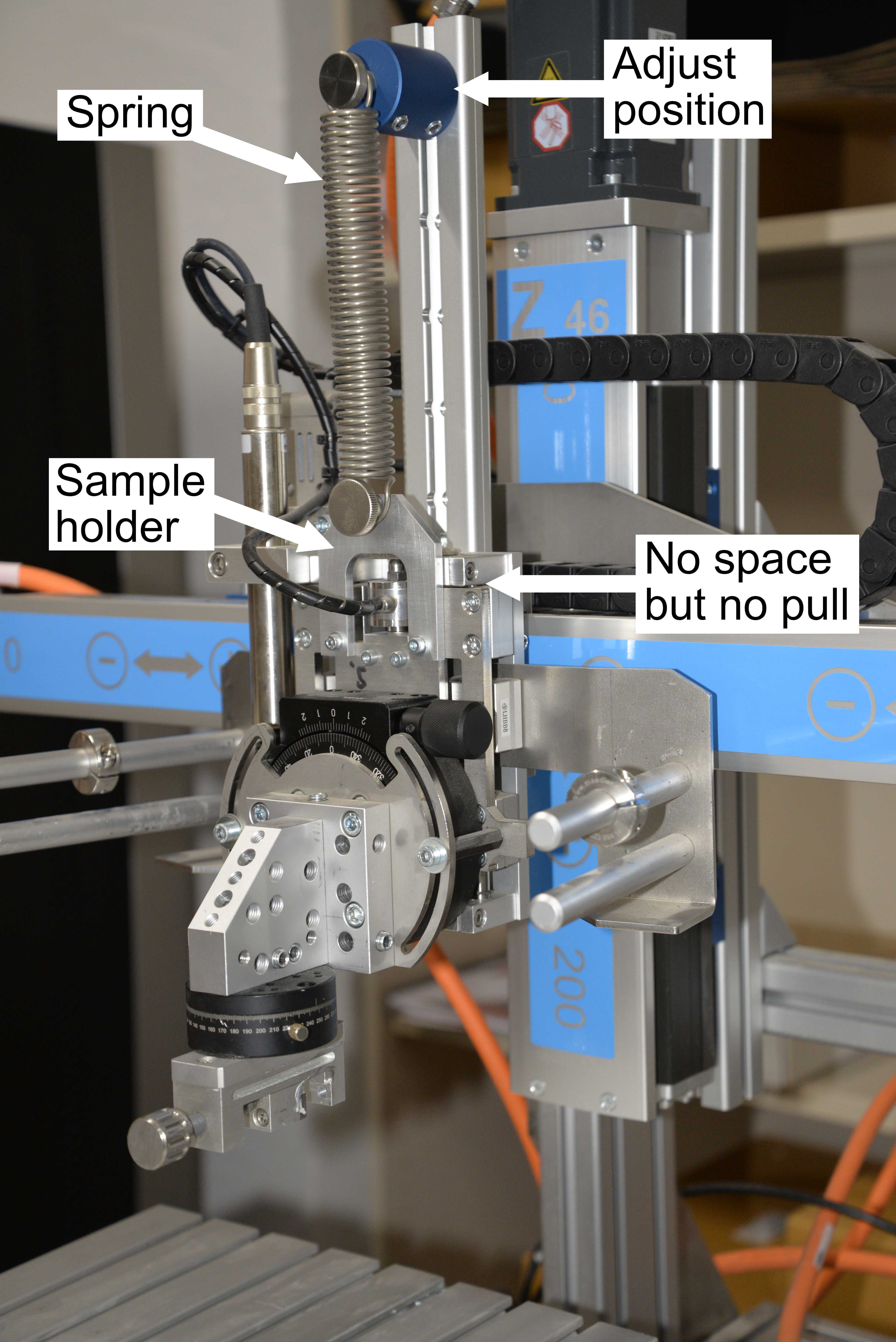
Setup sample
The experimental standard sample (step #2) was clamped in the sample holder (SMARTTESTER) and manually oriented in all directions.
a) cutting movement
the active edge was parallel to the contact material and the blade is mounted perpendicular to it
(90°
)
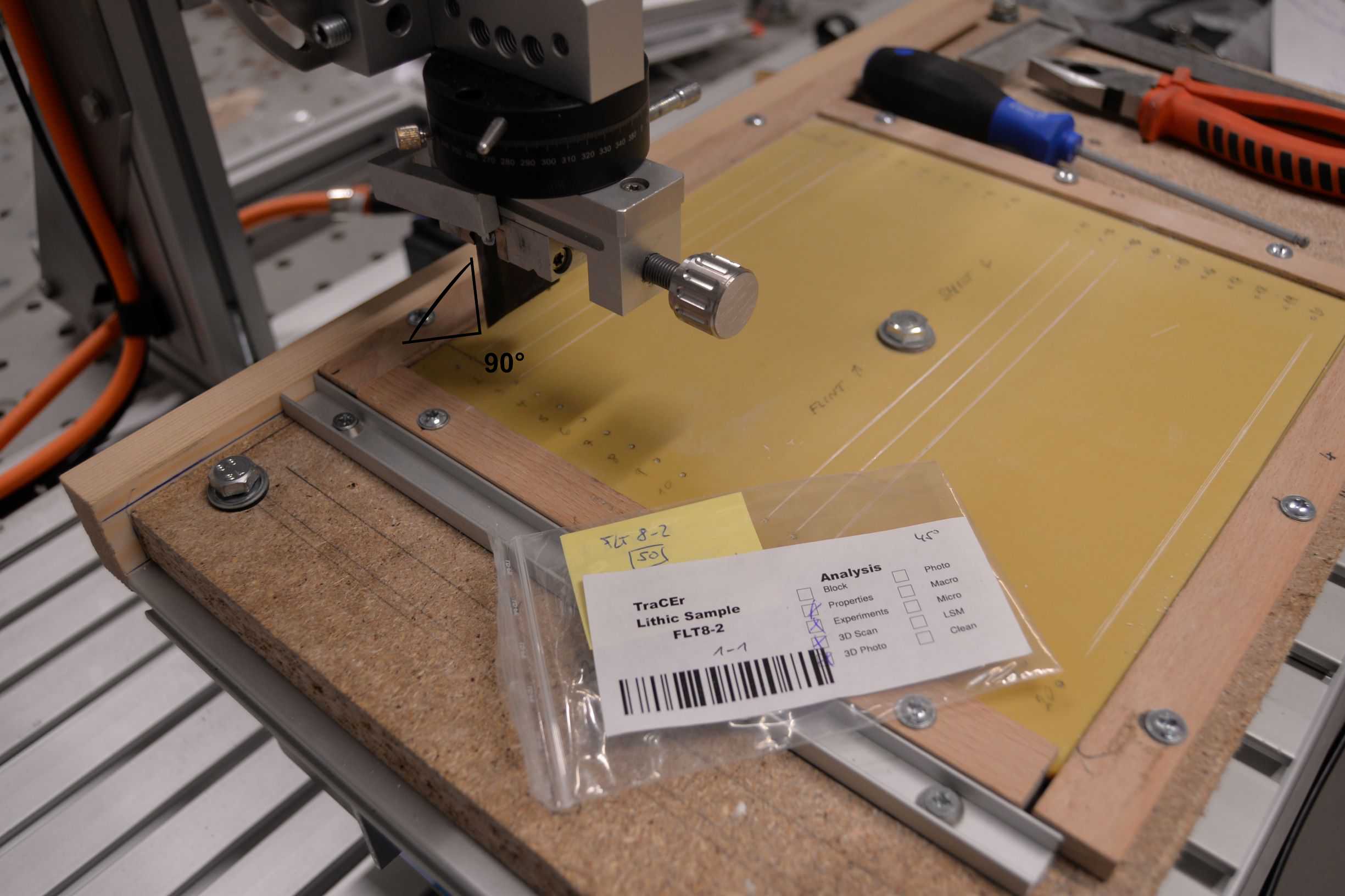
b) carving movement
the active edge was orientated in a flat angle towards the contact material (`20°` )
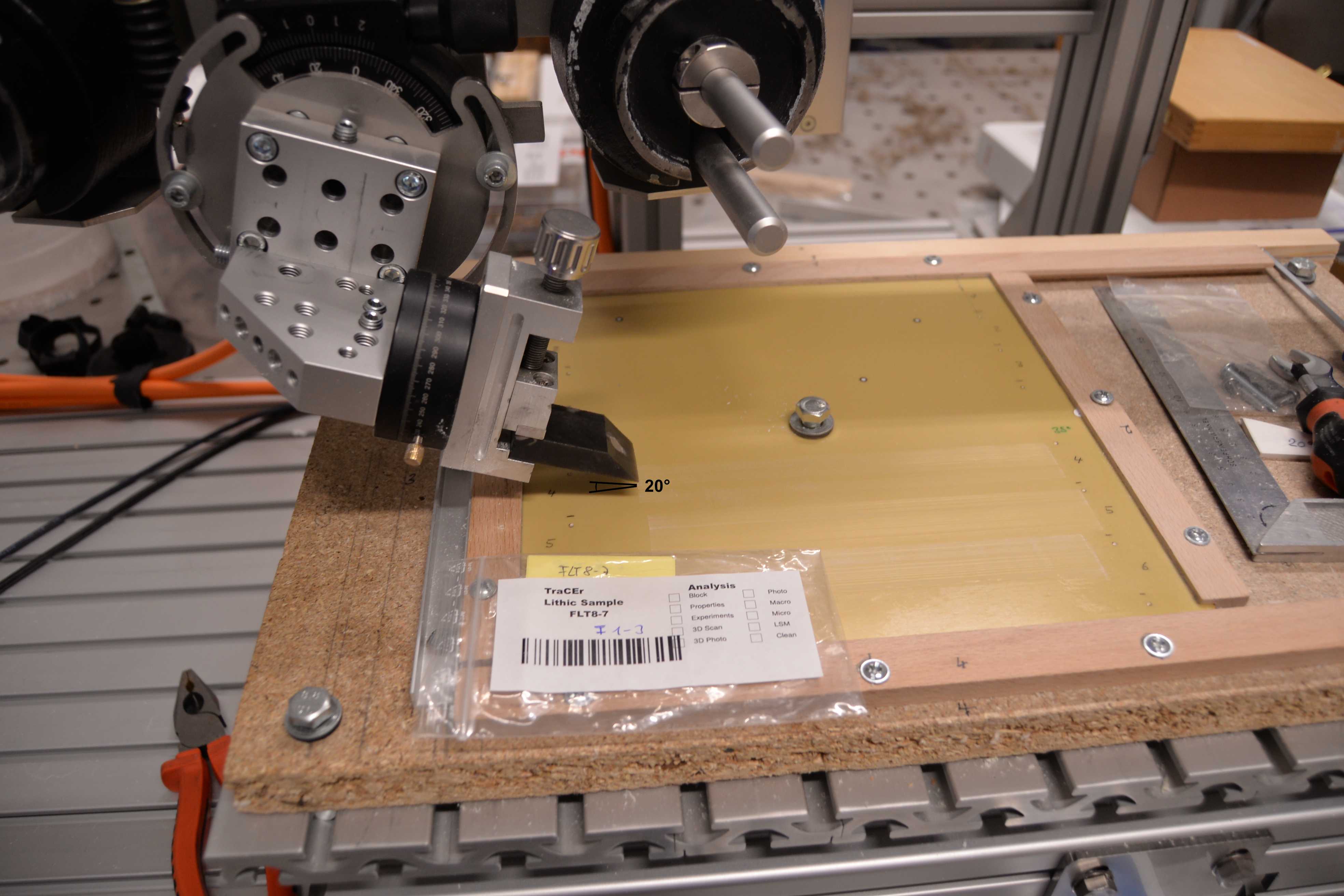
Setup contact material
The bone plates (step #3) were clamped in a custom-made sample holder and fixed with a screw in the middle of the bone plate (see photos in step #5.2).
The plate was aligned with the X-axis.
Program cutting and carving movement
The program is identical for cutting and carving. For each sample, a new template was created (named with the sample ID and the stroke number).
a) Move down in Z-direction to start position
The z-value of the starting point was defined as follows: the sample holder on the z-drive was moved down slowly until the edge of the sample was in contact with the bone plate. 5 mm were added to the position of the z-drive in order to give the sample the possibility to penetrate into the bone plate without cutting through the 6mm-thick bone plate.
b) Move forward in X-direction 170mm
(linear movement)
c) Move up in Z-direction approx. 20mm
(above bone plate; no contact between contact material and sample)
d) Move backwards in X-direction to starting point
e) Loop 50 times over steps #5.4a-5.4d and export data to CSV
f) Loop 200 times over steps #5.4a-5.4d and export data to CSV
g) Loop 750 times over steps #5.4a-5.4d and export data to CSV
h) Loop 1000 times over steps #5.4a-5.4d and export data to CSV
The experiment was planned as a sequential experiment. The 2000 strokes were therefore split into four sequences (steps #5.4e-h). The experimental standard samples were documented after each sequence (step #6).
For each sequence, five CSV files were exported, one for each recorded channel:
- Penetration depth as measured by the distance sensor in the sample holder.
- Force applied (Z-direction) as measured by the force sensor in the sample holder.
- Friction as measured by the force sensor on the stage for the contact material.
- Position of the X-drive (travel range).
- Velocity of the X-drive.
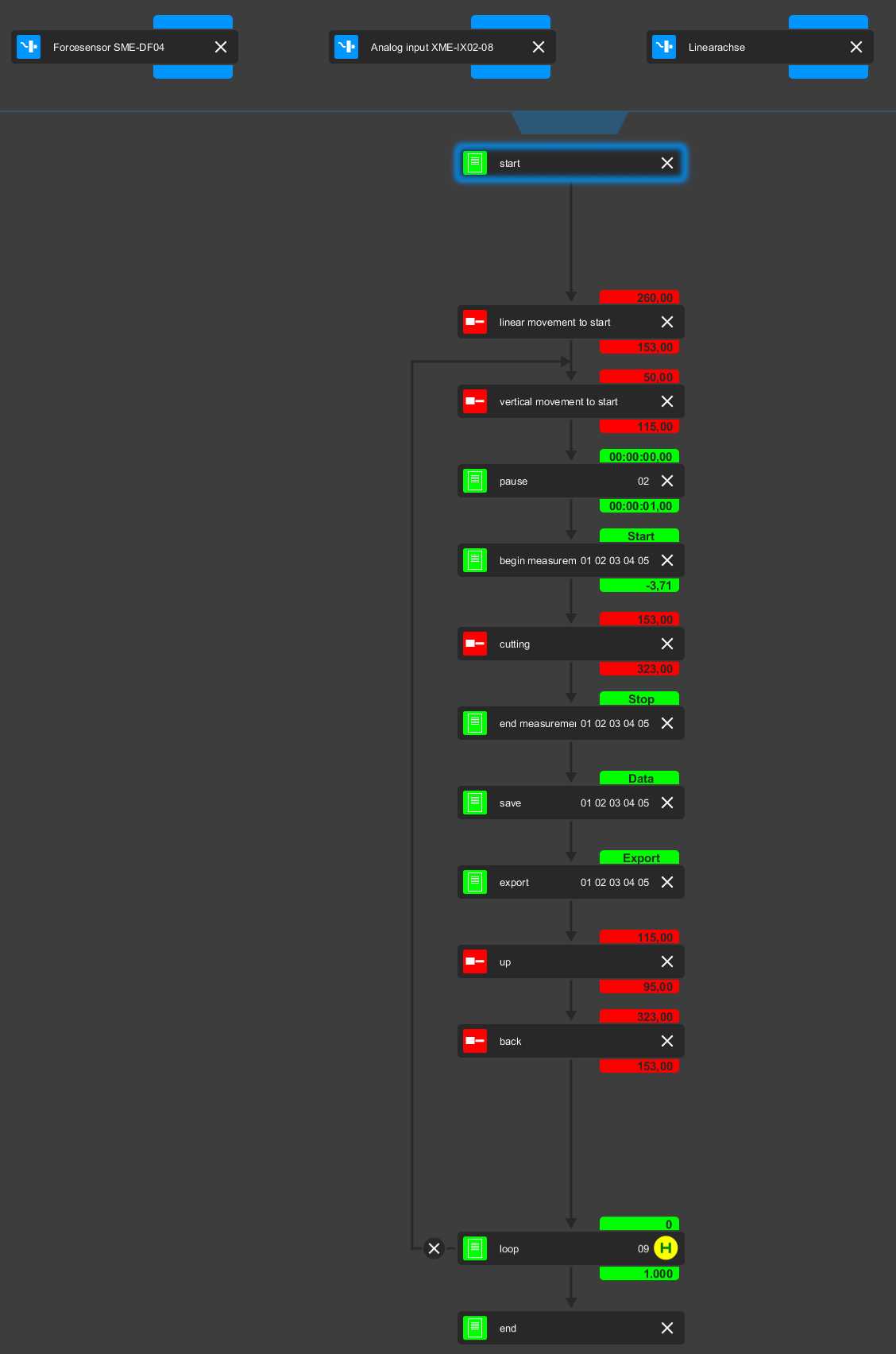
Program for sample FLT8-1 as example:
Run program
Each sample was used for a duration of ~ 7h 0m 0s
(= running time SMARTTESTER)
The following samples were used for the experiment:
Cutting 35° edge angle:
FLT8-4
FLT8-5
FLT8-6
LYDIT5-5
LYDIT5-6
LYDIT5-7
Cutting 45° edge angle:
FLT8-1
FLT8-2
FLT8-3
LYDIT5-2
LYDIT5-3
LYDIT5-4
Carving 35° edge angle:
FLT8-7
FLT8-8
FLT8-9
LYDIT5-11
LYDIT5-12
LYDIT5-13
Carving 45° edge angle:
FLT8-10
FLT8-11
FLT8-12
LYDIT5-8
LYDIT5-9
LYDIT5-10
Documentation
Sample documentation
Before the experiment as well as after each cycle all 24 samples were documented in an identical way following these steps:
- cleaning with tap water and commercial washing up liquid
- weight measurement (threefold repetition)
Equipment
Value | Label |
---|---|
Kern PCB 3500.2 | NAME |
weighing scale | TYPE |
Kern | BRAND |
- | SKU |
accuracy of 0.1g | SPECIFICATIONS |
- 3D scanning of all samples (identical settings for all scans; step #1.1)
- based on the 3D models, the volume of each sample could be calculated
Equipment
Value | Label |
---|---|
smartScan-HE R8 | NAME |
3D structured light scanner | TYPE |
AICON | BRAND |
- | SKU |
S-150 FOV, resolution of 33 µm | SPECIFICATIONS |
- 3D scanning of the contact material (only before and after 2000 strokes)
Equipment
Value | Label |
---|---|
smartScan-HE R8 | NAME |
3D structured light scanner | TYPE |
AICON | BRAND |
- | SKU |
M-450 FOV, resolution of 108 µm | SPECIFICATIONS |
- optical documentation of three of the four surfaces per sample (one lateral and the two main surfaces)
Equipment
Value | Label |
---|---|
Smartzoom 5 | NAME |
digital microscope | TYPE |
Zeiss | BRAND |
- | SKU |
PlanApo D 1.6x/0.10 objective; EDF-stitched images | SPECIFICATIONS |
- cleaning the area of interest with a cotton bud with
- cleaning the area of interest with a cotton bud with
- moulding of the two main sample surfaces with
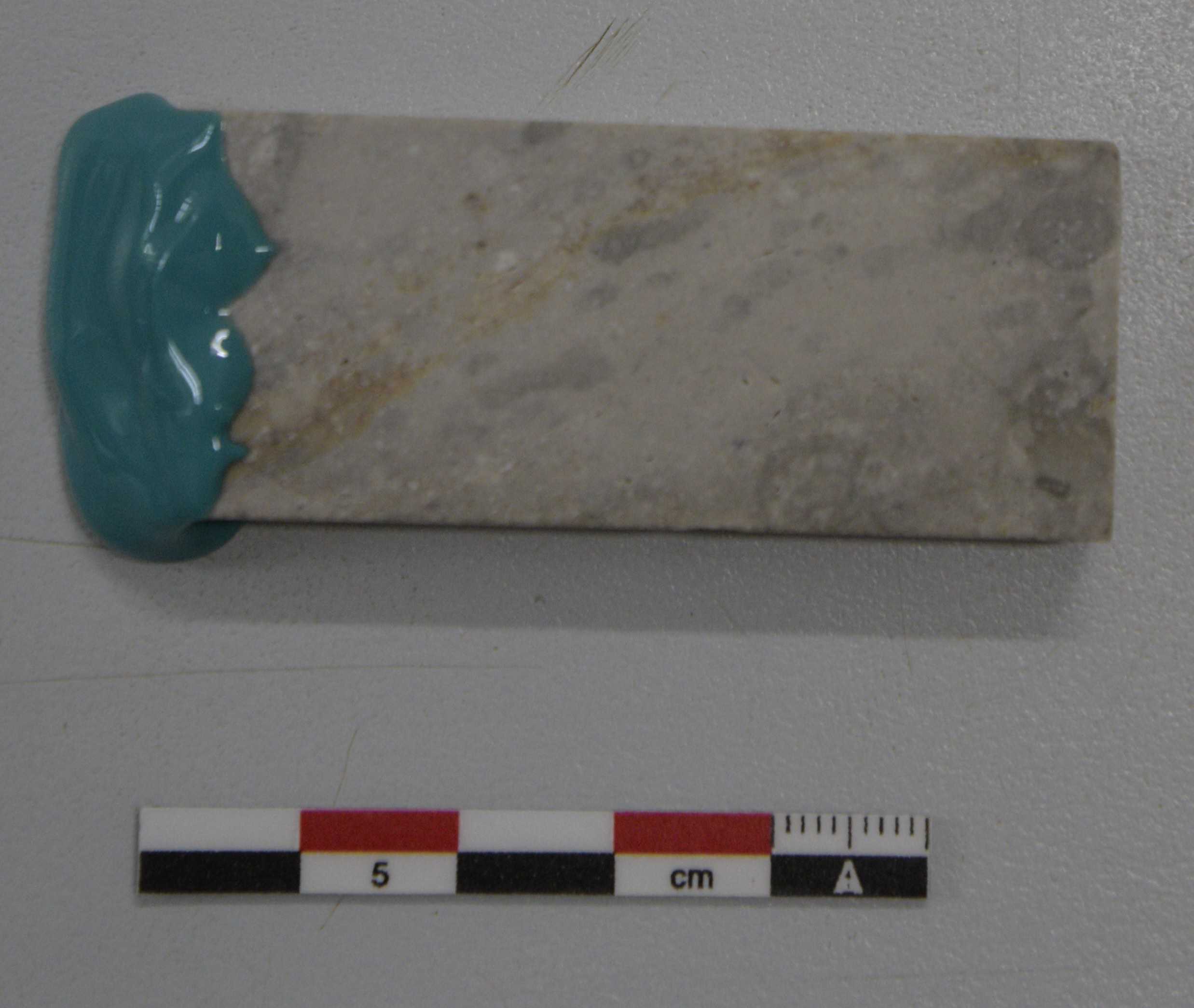
Data acquisition
After conducting the experiment and the final documentation of all experimental standard samples, further data was acquired:
- the edge angles of the samples
- the depth and width of the cuts and scratches on the artificial bone plate
Edge angle of the experimental standard samples
The 3D models (samples + contact material) were imported as STL files into GOM Inspect and existing mesh holes were closed. 3D models were edited as described in the previously mentioned protocol:
Software
Value | Label |
---|---|
GOM Inspect | NAME |
Hotfix 2, Rev. 111729, build 2018-08-22 | OS_NAME |
GOM | DEVELOPER |
https://www.gom.com/de-de/produkte/gom-inspect-suite | LINK |
2019 | VERSION |
Based on the closed models, the volume could be calculated.
Additionally, the edge angles of the samples after each cycle were calculated by means of GOM Inspect. To calculate the edge angle, 3D-EdgeAngle was applied again as for the archaeological artefacts (see step #1.2). Note that the parameters changed slightly ('3-points" instead of "2-lines" measuring procedure), since the "3-points" measuring procedure seems to be more suitable for simple morphologies as represented by the standard samples.
The following parameters were applied:
- "3-points" measuring procedure
- length of the line was defined with 2 mm
- as distance to the intersection the mean for distance three to six was calculated
- only sections two to eight were used
Penetration depth / dimensions of the grooves on the contact material
In addition, the contact material was documented with a Sensofar S-wide (Sensofar Metrology, Spain), a 3D optical metrology system. This way, the cuts and the scratches on the bone plate could be quantified.
Equipment
Value | Label |
---|---|
S wide | NAME |
3D optical metrology system | TYPE |
Sensofar | BRAND |
- | SKU |
- each bone plate was documented in four quadrants due to the limited travel range of the stage
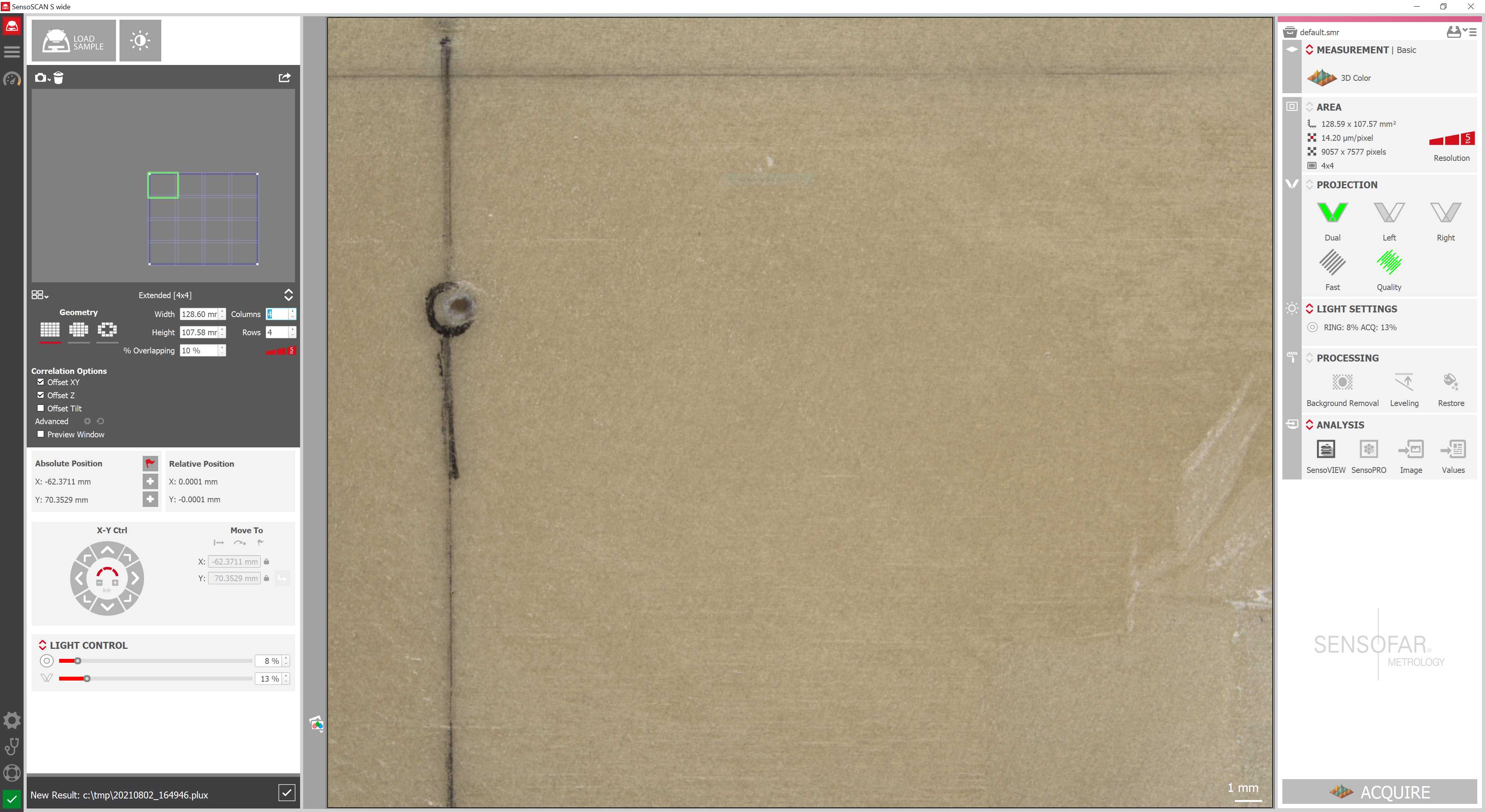
The data was processed in ConfoMap (a derivative of MountainsMap Imaging Topography developed by Digital Surf, Besançon, France; version ST 8.1.9286).
Software
Value | Label |
---|---|
ConfoMap (MountainsMap Imaging Tophography) | NAME |
Digital Surf, Besançon, France | DEVELOPER |
https://www.digitalsurf.com/de/ | LINK |
ST 8.1.9286 | VERSION |
In total, two templates were used:
a) "Patch surfaces of the bone plates acquired with the Sensofar S-wide"
An initial template was needed to patch the single quadrants together, so that the grooves are complete again. This involves levelling and aligning. Afterwards, each groove can be exported individually.
BP-I-TFE_S-wide_cutting_2000strokes_20210803_A-B.pdf
b) "Processing on single grooves"
This template extracts the topography layer of the grooves and calculates a mean profile of a series of 30 profiles. After levelling the mean profiles, the height and the width of each groove can be calculated.
BP-I-TFE_S-wide_cutting_2000strokes_20210803_FLT8-1_45deg.pdf
The ConfoMap templates for each surface in MNT and PDF formats are available in open access on Zenodo (https://doi.org/10.5281/zenodo.7565158). This also includes all original and processed surfaces.
Data analysis
Data analysis
The data acquired within the experiment was analysed in R.
Software
Value | Label |
---|---|
R Studio Desktop | NAME |
The R Studio, Inc. | DEVELOPER |
https://www.rstudio.com/products/RStudio/ | LINK |
1.1.463 | VERSION |
The different datasets were split in separate analyses:
a) "analysis_HLC"
This R script imports and plots the Leeb rebound hardness data acquired on the experimental standard samples (see step #2.3).
b) "analysis_EA"
This R script deals with the calculated edge angles from the experimental standard samples (see step #7.1).
c) "analysis_ST.all_sensors"
These R scripts contain the analysis of the data acquired with the five sensors connected to the SMARTTESTER (see step #5.4). However, plots concern only the data from the penetration depth.
d) "analysis_S.wide"
These R scripts deal with the penetration depth of the experimental standard samples into the contact material. The penetration depth is already part of "analysis_ST.all_sensors", but was additionally calculated with a Sensofar S-wide (see step #7.2).
e) "analysis_VW"
This R script contains the volume and the weight measurements for all experimental standard samples from before and after the experiment (see step #6).
The entire repository with all R analyses can be found on GitHub:
https://github.com/lschunk/PastHuman_StoneToolPerformance.git
and on Zenodo: