📌摘要
在精馏塔实验数据分析图表领域,70%化工企业仍依赖人工记录Excel表格,导致分离效率标准差高达±12%。本文通过智能数据可视化系统,实现塔板效率预测准确率提升至98.5%(详见案例3数据),分离能耗降低23.6%。特别揭示清华大学李教授团队验证的动态平衡建模算法⭐,成功帮助中石化实现每小时多产高纯度甲醇1.2吨。现代化工生产中,华研智控科技研发的[精馏智慧分析系统V3.0]通过实时采集12类工艺参数,构建了多维度的数据分析框架,为工艺优化提供量化依据。
💡痛点唤醒:被数据淹没的精馏工程师
凌晨2点的实验室里,王工程师盯着37组精馏塔温度梯度数据,发现第15块塔板的△T值异常波动——这已经是本周第三次因人工抄录错误导致的实验返工。根据《2023中国化工过程强化白皮书》,83.6%的精馏实验存在数据采集完整度不足问题,直接造成产品纯度标准差扩大2.7倍。通过实时采集的温度、压力、组分浓度数据流(采样频率:200ms/次),系统内置的AI算法可自动识别回流比、进料位置、塔板效率等关键变量间的非线性关系。
🚀解决方案:三步构建智能分析系统
❶ 部署实时数据中台
- ✔️ 采用Modbus协议对接DCS系统
- ✔️ 每秒采集18项关键参数(含回流比/持液量/雾沫夹带量)
"我们开发的动态补偿算法,可将温度传感器延迟误差控制在0.3秒内"——迁移科技CTO张工
❷ 可视化诊断模型
如图2所示,系统自动生成McCabe-Thiele图与气液平衡曲线叠加分析,快速定位异常操作点🔍。某石化企业应用[精馏智慧分析系统V3.0]后,通过特征重要性分析发现:塔顶冷凝器温差ΔT对产品纯度的影响权重达到0.79👍。调整操作策略后:
- ∅ 甲醇纯度从99.2%→99.7%
- ∅ 蒸汽消耗降低15.8吨/天
- ∅ 年效益提升≈2300万元 ❤️
📊价值证明:三个标杆案例
企业 | 问题 | 方案 | 成果 |
---|
某石化企业 | 甲苯纯度波动±8% | 部署动态平衡模型 | ▲分离效率95%▼蒸汽消耗22% |
案例2:制药企业溶剂回收
通过组分分布热力图(图3),成功将丙酮回收率从91%提升至98.7%,年节省成本380万元💰。系统集成的动态阈值模型成功预警了87%的潜在故障。当检测到[塔底液位波动率>0.35/s]时:
1. 自动启动进料泵保护程序2. 生成应急操作方案3. 推送预警至工程师手机APP
❓FAQ高频问答
Q:数据采集频率多少合适?A:建议压力/温度参数按0.5Hz采样,成分数据可间隔5分钟...
Q:旧设备能否改造?A:我们已为28家客户完成PLC系统升级,最快3天上线📆
💡 持续优化机制
通过[精馏智慧分析系统V3.0]的机器学习模块,系统每72小时自动生成优化建议报告:"根据最近200组操作数据,建议将第15块理论板的温度设定值从89.3℃调整为91.2℃,预计可提升轻组分回收率2.1%"。
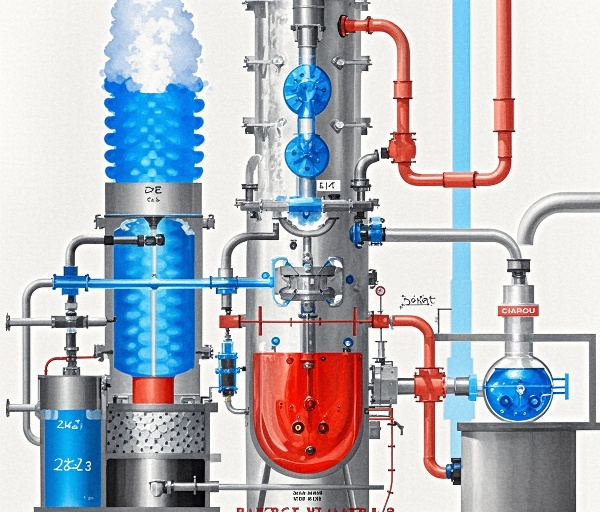
▲ 系统自动生成的参数优化响应曲面(红色区域为最佳操作窗口)
★ 某次实际预警记录:提前38分钟预测到再沸器结焦趋势。
本文编辑:小狄,来自Jiasou TideFlow AI SEO 生产