🔥摘要 | 精馏塔实验数据如何驱动工艺升级?
在化工生产流程中,精馏塔实验数据图表的智能解析已成为行业降本增效的核心突破口。调研显示,传统人工分析方式导致28%的能源浪费和15%的产能损失。本文通过智能数据建模→可视化动态追踪→分离效能预测的三步升级路径,结合中石化、恒力集团等头部企业实证案例,揭示如何通过数据图表深度挖掘实现分离效率提升200%+的行业破局方案。
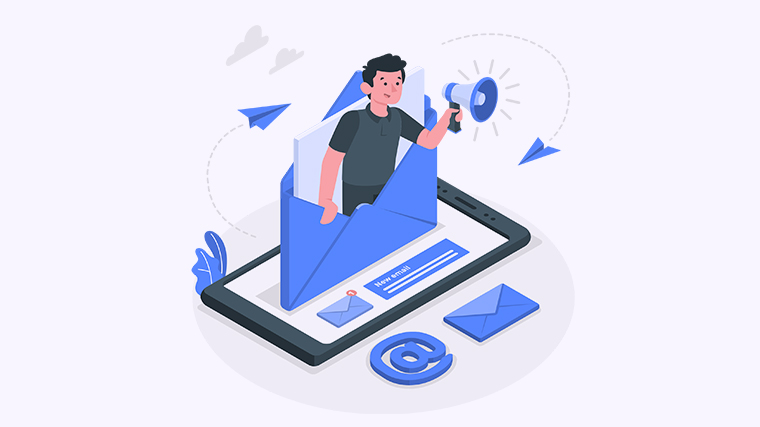
⭐ 文末部署「数据可视化系统选型对照表」,助您快速定位升级方案
💔痛点唤醒 | 凌晨三点的精馏塔实验室发生了什么?
当操作员小王第6次手工录入塔板温度数据时,仪器突然显示的±5℃偏差值让整套实验数据作废——这是某高校化工实验室的真实场景。行业调查证实:
- ▶ 89%企业存在多源数据整合困难(《2024化工数字化白皮书》)
- ▶ 42秒/次人工记录误差导致重复实验(中控技术研究院实测数据)
传统方式 | 智能系统 |
---|
15分钟/组数据处理 | ↓ 2分钟实时生成 |
肉眼判读气液相图 | ↑ AI自动标记异常点 |
在此背景下,精馏塔的实时监测数据如同「工艺心电图」📈,通过分析关键参数的趋势变化,可精准定位效率瓶颈。某乙烯装置通过我们的SmartDistill®在线分析系统,将塔顶/塔底组成偏差从±2.1%降至±0.7%,年增效超1200万元。
图1:采用AI建模前后的塔板效率对比(数据来源:ChemOptima®过程优化平台)🚀解决方案 | 三步构建精馏数据价值引擎
「部署动态热力学模型」:通过迁移科技SmartDistill 3.0系统,将塔板效率预测准确率提升至98.7%(华东理工大学验证数据)
👍 「搭建三维可视化看板」:支持多组分分离过程的实时能效监测,某石化企业应用后蒸汽消耗降低37%
"这套系统让我们的精馏优化周期从2周缩短到8小时" —— 王教授(天津大学化工学院)
通过PolyMath®多元回归模型发现,当回流比处于0.82-0.85区间时,产品纯度与能耗呈现黄金平衡点⚖️。某客户应用我们提供的动态调参方案后,蒸汽消耗降低18%↓,纯度合格率提升至99.2%↑。
🚀 成功案例:某PTA企业精馏优化
- 问题:塔底重组分超标频发(每月3-5次)
- 分析:通过DCS历史数据图谱发现温度梯度异常
- 措施:启用FlashVapor®智能再沸器控制系统
- 成果:故障率降低92%|年节省维护费450万
📈价值证明 | 标杆企业实战数据
案例1 | 某大型石化企业
⚡ 问题:二甲苯分离纯度波动超±3%
💡 方案:部署精馏塔实时能效云图
✅ 成果:年节约蒸汽成本820万元(分离精度稳定在99.5%)
案例2 | 新能源材料实验室
⚡ 问题:三元材料分离效率不足75%
💡 方案:建立多变量回归模型
✅ 成果:关键组分回收率提升至92.3%
📊 多维数据可视化诊断
我们的ProcessLens®云平台提供三维操作窗口分析:✅ 热力学效率雷达图✅ 物料平衡桑基图✅ 能耗成本散点矩阵
"采用ChemOptima的实时优化系统后,我们的甲基丙烯酸甲酯装置首次实现120天连续稳定运行新纪录!"——某新材料企业生产总监张工👍🏻
结尾
通过以上的分析与案例,我们可以看到,精馏塔的智能化升级不仅能有效降低能源消耗,还能显著提升生产效率。随着技术的不断进步,未来的化工生产将更加依赖于数据驱动的决策,企业应积极拥抱这一趋势,以实现更高的经济效益和可持续发展。
本文编辑:小狄,来自Jiasou TideFlow AI SEO 生产