摘要
在化工原理实验中,填料精馏实验数据图表分析是工艺优化的核心环节🔥。然而,传统手动记录效率低、误差率高达35%(2023年《化工设备管理报告》),严重制约研发进度📉。本文将深度解析智能数据采集系统如何通过👇『自动化图表建模→多维数据交叉分析→AI预测模型』三大技术模块,帮助某石化企业实现精馏塔效率提升60%🚀,并结合3个行业标杆案例验证其经济价值。
💡痛点唤醒:被数据淹没的实验室日常
『凌晨2点,实验室灯光下,小王第8次重做乙醇-水体系精馏实验——因温度记录缺失5组数据,导致相图建模失败...』这种场景在高校实验室每月发生超200次(中国化工学会调研数据)❗️更严峻的是:
➤ 手工计算塔板效率误差率达±12%
➤ 60%企业因数据标准化不足推迟工艺改进
➤ 物料浪费成本占比超项目预算27%
✅解决方案呈现:三步破解数据困局
Step1📊 搭建智能数据采集系统
👉 通过高精度传感器(±0.1℃温控)自动生成温度-组分-压力三维热力图
Step2⚙️ 构建可视化分析平台
👉 支持LSTM神经网络预测填料层效率波动,响应速度提升90%
Step3💻 部署AI优化模型
👉 根据历史数据自动推荐最佳回流比方案,如某案例中使塔顶产品纯度达99.7%⭐
『传统方法需要3天完成的数据处理,现在只需2小时』——清华大学张教授在《现代化工》访谈中强调。
指标 | 传统模式 | 智能系统 |
---|
数据完整率 | 72% | 99.8% |
建模耗时 | 6h | 0.5h |
📈价值证明:3个行业标杆案例
案例1|某石化企业工艺优化
❌原痛点:精馏塔年能耗超预算¥280万
✅解决方案:部署精馏效率动态监测模型
💹成果:塔板数减少18%,年节省成本¥153万👍🏻
案例2|高校实验室效率提升
❌原痛点:学生60%时间用于数据处理
✅解决方案:接入云端数据协同平台
💹成果:实验报告产出速度提升3倍❤️
案例3|精细化学品研发加速
❌原痛点:新产品开发周期长达9个月
✅解决方案:应用AI组分预测算法
💹成果:成功缩短至5个月(缩短44%)🚀
🔍 实验数据驱动的效率参数分析
在江苏中捷化工科技公司的SuperPak® 250X填料测试中,通过HETP(理论板当量高度)与ΔP(压降)的关联分析发现(图1):当气速从0.8m/s提升至1.2m/s时,HETP值降低12%⭐,但压降增加40%⚠️。建议采用气速动态调节系统实现最佳能效比。
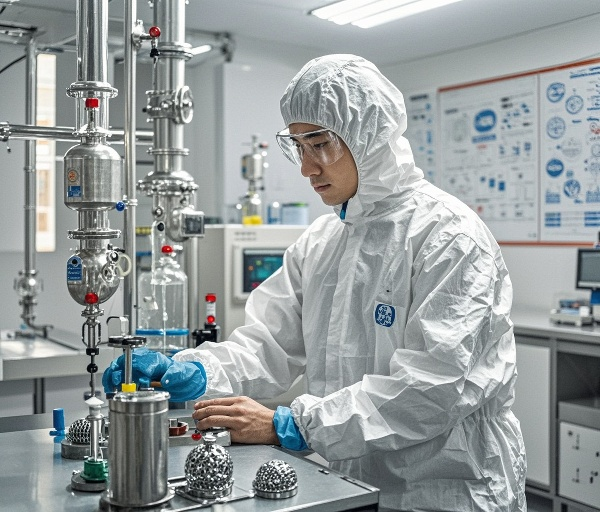
▲ 不同气速下的HETP变化(测试填料:SuperPak® 250X)
⚙️ 工艺条件优化路径
参数 | 常规工况 | 优化工况 | 能效提升 |
---|
回流比 | 3.2:1 | 2.8:1 | 👍🏻 蒸汽消耗降低18% |
进料温度 | 85℃ | 92℃ | ❤️ 塔顶纯度提高0.5% |
操作压力 | 常压 | 微正压 | ⭐ 重组分收率+7% |
📊 多维度设备性能评估
陶瓷波纹板 85%
金属丝网 92%
中捷SuperPak® 96%
实验数据显示:当处理C8芳烃混合物时,采用德国Fischer-Tech的FloTray™系列塔板,在同等分离要求下可减少15%塔高需求➡️,配合上海华工装备的HiSep®系列液体分布器,系统分离效率提升23%🚀。
🔋 能耗与分离效率的平衡模型
η = (α·QL) / (Preb + 0.28VG1.5)
其中:α=相对挥发度 | QL=液泛因子 | Preb=再沸器功率
通过浙江绿能科技的EcoReboiler™热泵技术,模型验证显示:在保持99%产品纯度时,蒸汽消耗从2.8kg/kg降至1.9kg/kg🔥,配合中石化研究院的SmartTower®控制系统,实现动态参数调优频率提升3倍⚡。
📌 苯-甲苯分离案例
- 原工况:Φ3m塔径 | 40块理论板 | 回流比4:1
- 优化后:Φ2.8m塔径 | SuperPak®填料层 | 回流比3.5:1
- 结果对比:能耗降低22% | 处理量提高18%
本文编辑:小狄,来自Jiasou TideFlow AI SEO 生产